Термиялық аударым технологиясы - косметикалық қаптама материалдарын беткі өңдеудегі жалпы процесс. Бұл брендтермен басып шығаруға ыңғайлы, өйткені оның басып шығарудағы ыңғайлылығы мен үлгілер мен үлгілер. Алайда, термиялық аударым технологиясы сонымен қатар сапалы мәселелер жиі кездеседі. Осы мақалада біз кейбір жалпы сапа проблемалар мен шешімдерді тізімдіміз.
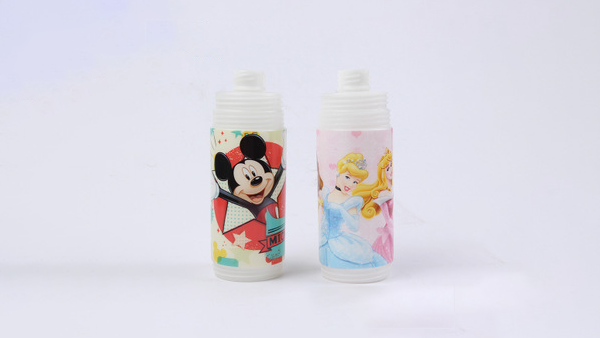
Жылуды беру технологиясы газбен немесе бояғыштармен қапталған, ол орташа мөлшердегі сия қабығының немесе бояғыштармен қапталған ауыстырғышты, ол термиялық аударым арқылы субстратқа және т.б. Сиямен қапталған ортаға субстратпен байланысыңыз. Термиялық басып шығару механизмі мен қысыммен жылу және қысым арқылы, ортадағы сия қалаған өнімді алу үшін балқып, субстратқа жіберіледі.
1, толық парақ гүлі
Құндылық: Дақтар мен үлгілер толық бетте пайда болады.
Себебі: сияның тұтқырлығы тым төмен, қырғыштың бұрышы дұрыс емес, сияның кептіру температурасы жеткіліксіз, статикалық электрмен және т.б.
Ақаулықтарды жою: Тұтқырлықты арттыру, қырғыштың бұрышын реттеп, пештің температурасын жоғарылатыңыз және пленканың артқы жағын статикалық агентпен алдын ала палатаңыз.
2. Тарту
Құндылық: Кірі тәрізді сызықтар, әдетте, ақ сиямен және үлгінің шетінен пайда болады.
Себебі: сия пигментінің бөлшектері үлкен, сия таза емес, тұтқырлық жоғары, статикалық электр және т.б.
Ақаулықтарды жою: Концентрацияны азайту үшін сияны сүзіп, қырғышты алыңыз; Ақ сияны алдын-ала қайратуға болады, пленканы статикалық электрмен өңделуге болады, ал қырғыштар мен картиналарды өткір таяқшамен сындыруға болады немесе статикалық агент қосуға болады.
3. Түстерді тіркеу және түбінің асты
Құндылық: Бірнеше түстер бірнеше түрлі-түсті болса, түрлі-түсті топтың ауытқуы, әсіресе түс түсінде пайда болады.
Негізгі себептері: машинаның өзі дәлдік пен ауытқуларға ие; Нақты тақтайшалар; өңдік түс пен жиырылудың дұрыс еместігі.
Ақаулықтарды жою: қолмен тіркеу үшін строб шамдарын қолданыңыз; Пле-тақтай жасау; Үлгідің визуалды әсерінің әсерінен кеңейіп, келісімшарт немесе өрнектің кішкене бөлігін ағызмаңыз.
4. Сияны анық сындырмайды
Феноменон: басылған қабықша тұман пайда болады.
Себеп: қырғышты бекіту жақтауы бос; Плитаның беті таза емес.
Ақаулықтарды жою: қырғышты реттеп, пышақ ұстағышты бекітіңіз; Баспа табақшасын тазалаңыз және қажет болса, жуғыш зат ұнтағын қолданыңыз; Пластиналар мен қырғыштардың арасында кері әуе беру орнатыңыз.
5. Түс қабыршақтары
Феномен: Түс салыстырмалы түрде үлкен өрнектердің жергілікті бөліктерінде, әсіресе тазартылған әйнек пен тот баспайтын болаттан жасалған жерлерде орналасады.
Себебі: өңделген пленкада басып шығарылған кезде түс қабаты әлдеқайда көп; Статикалық электр; Түс сия қабаты қалың және кептірілмейді.
Ақаулықтарды жою: Пештің температурасын арттырыңыз және жылдамдықты азайтыңыз.
6. Тасымалдаудың нашарлығы
Құндылық: субстратқа жіберілген түс қабаты сынақ таспасынан оңай шығарылады.
Себебі: субстратқа сәйкес келмейтін арқалық желіммен жасалған дұрыс бөліну немесе артқы желім.
Ақаулықтарды жою: Бөлу желімін ауыстырыңыз (қажет болса реттеңіз); Субстратқа сәйкес келетін артқы желімді ауыстырыңыз.
7. Жабысқақ
Феноменон: Кері кету кезінде сия қабаты сөніп, дыбыс қатты.
Себебі: орамалды кернеу, инспекцияны толық құрғатыңыз, инспекция кезінде тым қалың затбелгі, температура мен ылғалдылық нашар, статикалық электр, тым жылдам басып шығару жылдамдығы және т.б.
Ақаулықтарды жою: орамалды кернеуді азайту немесе басып шығару жылдамдығын тиісті түрде азайтыңыз, кептіруді аяқтаңыз, жабық температура мен ылғалдылықты бақылау және статикалық агентке алдын-ала қолдануға болады.
8. Нүктелерді тастау
Феноменон: Таяз торда тұрақты емес ағып жатқан нүктелер пайда болады (басып шығару мүмкін емес нүктелерге ұқсас).
Себебі: сияны қою мүмкін емес.
Ақаулықтарды жою: Орналасуды тазалаңыз, электростатикалық сия сорғыш роликтерін қолданыңыз, нүктелерді тереңдеңіз, қырғыштың қысымын реттеңіз және сия тұтқырлығын басқа шарттарға әсер етпей азайтыңыз.
9. Алтын, күміс және меруертсцентті басып шығарылған кезде апельсин қабығы тәрізді тәрізді
Феноменон: Алтын, күміс және інжу-маржан, әдетте, үлкен аймақта апельсин қабығы тәрізді сызаттар бар.
Себебі: алтын, күміс және меруертсценттің бөлшектері үлкен және сия науасында біркелкі таралуы мүмкін емес, нәтижесінде тығыздыққа әкеледі.
Ақаулықтарды жою: басып шығарудан бұрын, сияны біркелкі араластырыңыз, сияны сия науасына сорып, сия науасына пластикалық ауа үрлегін салыңыз; басып шығару жылдамдығын азайтыңыз.
10. Басып шығарылған қабаттардың нашар репродукциясы
Құбылыс: қабаттарда тым үлкен өрлеу (мысалы, 15% -100% -100%), көбінесе жарық бөлігінде басып шығарылмайды, қараңғы реңк бөлігінде жеткіліксіз, немесе ортаңғы реңк бөлігінде, анық Жеңіл және қараңғы.
Себебі: нүктелердің өтпелі ауқымы тым үлкен, ал сияның фильмге адгезиясы нашар.
Ақаулықтарды жою: электростатикалық сия сіңіретін роликті қолданыңыз; Екі табаққа бөліңіз.
11. Басып шығарылған өнімдерге жарық жылтырлығы
Құндылық: Басып шығарылған өнімнің түсі үлгіні, әсіресе күмісті басып шығарған кезде жеңілірек.
Себеп: Сия тұтқырлығы тым төмен.
Ақаулықтарды жою: сияның тұтқырлығын тиісті мөлшерге дейін арттыру үшін түпнұсқа сия қосыңыз.
12. Ақ кейіпкерлердің жиектері бұралған
ҚұнымON: Жазылған жиектер көбінесе жоғары сапалы таңбалардың жиектерінде пайда болады.
Себебі: Сияның гранулярлығы мен пигменті жеткіліксіз; Сияның тұтқырлығы төмен, т.б.
Жою: пышақты қайрау немесе қоспалар қосу; Мектерлердің бұрышын реттеу; сияның тұтқырлығын арттыру; Электр дақылдарын пластинаны лазер тақтасына ауыстыру.
13. Тот баспайтын болаттан жасалған (кремниймен қапталған) алдын-ала қапталған пленканың біркелкі емес жабыны
Тот баспайтын болаттан жасалған пленканы басып шығармас бұрын, пленка әдетте алдын-ала өңделеді (кремний жабыны). Фильмдегі сия қабаты).
Феноменон: Фильмде сызықтар мен жіптер бар.
Себебі: температура жеткіліксіз (кремнийдің жеткіліксіз ыдырауы), еріткіш коэффициенті.
Жою: пештің температурасын белгіленген биіктікке көбейтіңіз.
POST TIME: JUL-03-2024