Introduction: Acrylic bottles have the characteristics of plastic, such as resistance to falling, light weight, easy coloring, easy processing, and low cost, and also have the characteristics of glass bottles, such as beautiful appearance and high-end texture. It allows cosmetics manufacturers to obtain the appearance of glass bottles at the cost of plastic bottles, and also has the advantages of resistance to falling and easy transportation.
Product Definition
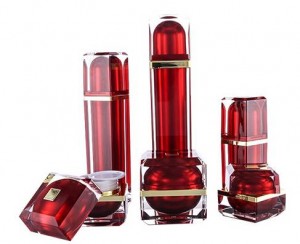
Acrylic, also known as PMMA or acrylic, is derived from the English word acrylic (acrylic plastic). Its chemical name is polymethyl methacrylate, which is an important plastic polymer material that was developed earlier. It has good transparency, chemical stability and weather resistance, is easy to dye, easy to process, and has a beautiful appearance. However, since it cannot come into direct contact with the cosmetics, acrylic bottles usually refer to plastic containers based on PMMA plastic materials, which are formed by injection molding to form a bottle shell or lid shell, and combined with other PP and AS material liner accessories. We call them acrylic bottles.
Manufacturing process
1. Molding Processing
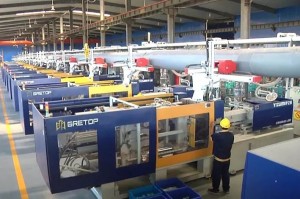
Acrylic bottles used in the cosmetics industry are generally molded by injection molding, so they are also called injection-molded bottles. Due to their poor chemical resistance, they cannot be directly filled with pastes. They need to be equipped with inner liner barriers. Filling should not be too full to prevent the paste from entering between the inner liner and the acrylic bottle to avoid cracking.
2. Surface treatment
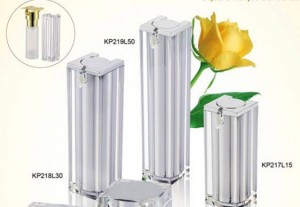
In order to effectively display the contents, acrylic bottles are often made of solid injection color, transparent natural color, and have a sense of transparency. Acrylic bottle walls are often sprayed with color, which can refract light and has a good effect. The surfaces of matching bottle caps, pump heads and other packaging materials often adopt spraying, vacuum plating, electroplated aluminum, wire drawing, gold and silver packaging, secondary oxidation and other processes to reflect the personalization of the product.
3. Graphic printing
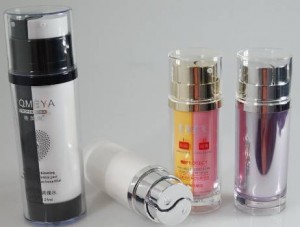
Acrylic bottles and matching bottle caps are usually printed by silk screen printing, pad printing, hot stamping, hot silver stamping, thermal transfer, water transfer and other processes to print the company's graphic information on the surface of the bottle, bottle cap or pump head.
Product Structure
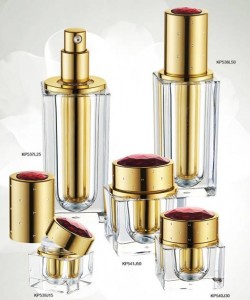
1. Bottle type:
By shape: round, square, pentagonal, egg-shaped, spherical, gourd-shaped, etc. According to the purpose: lotion bottle, perfume bottle, cream bottle, essence bottle, toner bottle, washing bottle, etc.
Regular weight: 10g, 15g, 20g, 25g, 30g, 35g, 40g, 45g Regular capacity: 5ml, 10ml, 15ml, 20ml, 30ml, 50ml, 75ml,
100ml, 150ml, 200ml, 250ml, 300ml
2. Bottle mouth diameter Common bottle mouth diameters are Ø18/410, Ø18/415, Ø20/410, Ø20/415, Ø24/410, Ø28/415, Ø28/410, Ø28/415 3. Bottle body accessories: Acrylic bottles are mainly equipped with bottle caps, pump heads, spray heads, etc. Bottle caps are mostly made of PP material, but there are also PS, ABC and acrylic materials.
Cosmetic applications
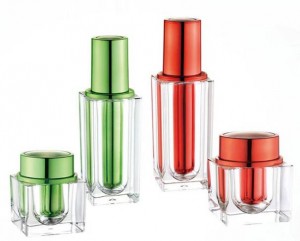
Acrylic bottles are widely used in the cosmetics industry.
In skin care products, such as cream bottles, lotion bottles, essence bottles, and water bottles, acrylic bottles are used.
Purchase precautions
1. Minimum order quantity
The order quantity is generally 3,000 to 10,000. The color can be customized. It is usually made of primary frosted and magnetic white, or with pearlescent powder effect. Although the bottle and the cap are matched with the same masterbatch, sometimes the color is different due to the different materials used for the bottle and the cap.2. The production cycle is relatively moderate, about 15 days. Silk-screen cylindrical bottles are calculated as single colors, and flat bottles or special-shaped bottles are calculated as double or multi-colors. Usually, the first silk-screen screen fee or fixture fee is charged. The unit price of silk-screen printing is generally 0.08 yuan/color to 0.1 yuan/color, the screen is 100 yuan-200 yuan/style, and the fixture is about 50 yuan/piece. 3. Mold cost The cost of injection molds ranges from 8,000 yuan to 30,000 yuan. Stainless steel is more expensive than alloy, but it is durable. How many molds can be produced at a time depends on the production volume. If the production volume is large, you can choose a mold with four or six molds. Customers can decide for themselves. 4. Printing instructions The screen printing on the outer shell of acrylic bottles has ordinary ink and UV ink. UV ink has better effect, gloss and three-dimensional sense. During production, the color should be confirmed by making a plate first. The screen printing effect on different materials will be different. Hot stamping, hot silver and other processing techniques are different from the effects of printing gold powder and silver powder. Hard materials and smooth surfaces are more suitable for hot stamping and hot silver. Soft surfaces have poor hot stamping effects and are easy to fall off. The gloss of hot stamping and silver is better than that of gold and silver. Silk screen printing films should be negative films, the graphics and text effects are black, and the background color is transparent. Hot stamping and hot silver processes should be positive films, the graphics and text effects are transparent, and the background color is black. The proportion of text and pattern cannot be too small or too fine, otherwise the printing effect will not be achieved.
Product display
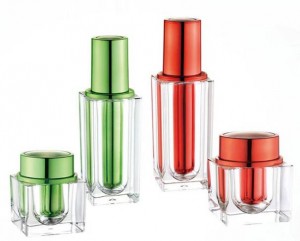
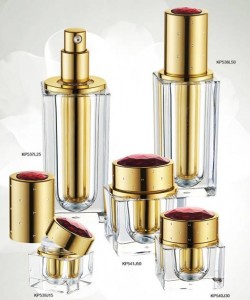
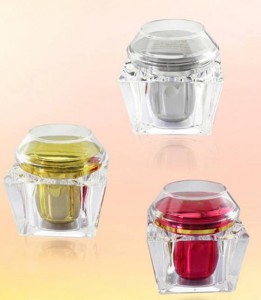
Post time: Sep-14-2024