Hose, a convenient and economical packaging material, is widely used in the field of daily chemicals and is very popular. A good hose can not only protect the contents, but also improve the product level, thus winning more consumers for daily chemical companies. So, for daily chemical companies, how to choose high-quality plastic hoses that are suitable for their products? The following will introduce several important aspects.
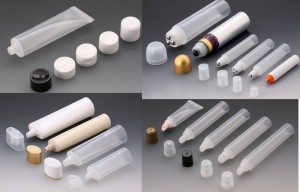
The selection and quality of materials are the key to ensuring the quality of hoses, which will directly affect the processing and final use of hoses. The materials of plastic hoses include polyethylene (for tube body and tube head), polypropylene (tube cover), masterbatch, barrier resin, printing ink, varnish, etc. Therefore, the selection of any material will directly affect the quality of the hose. However, the choice of materials also depends on factors such as hygiene requirements, barrier properties (requirements for oxygen, water vapor, fragrance preservation, etc.), and chemical resistance.
Selection of pipes: First, the materials used must meet the relevant hygiene standards, and harmful substances such as heavy metals and fluorescent agents should be controlled within the prescribed range. For example, for hoses exported to the United States, the polyethylene (PE) and polypropylene (PP) used must meet the US Food and Drug Administration (FDA) standard 21CFR117.1520.
Barrier properties of materials: If the contents of the packaging of daily chemical companies are some products that are particularly sensitive to oxygen (such as some whitening cosmetics) or the fragrance is very volatile (such as essential oils or some oils, acids, salts and other corrosive chemicals), five-layer co-extruded tubes should be used at this time. Because the oxygen permeability of the five-layer co-extruded tube (polyethylene/adhesive resin/EVOH/adhesive resin/polyethylene) is 0.2-1.2 units, while the oxygen permeability of the ordinary polyethylene single-layer tube is 150-300 units. In a certain period of time, the weight loss rate of the co-extruded tube containing ethanol is dozens of times lower than that of the single-layer tube. In addition, EVOH is an ethylene-vinyl alcohol copolymer with excellent barrier properties and fragrance retention (the thickness of 15-20 microns is the most ideal).
Material stiffness: Daily chemical companies have different requirements for the stiffness of hoses, so how to obtain the desired stiffness? The polyethylene commonly used in hoses is mainly low-density polyethylene, high-density polyethylene, and linear low-density polyethylene. Among them, the stiffness of high-density polyethylene is better than that of low-density polyethylene, so the desired stiffness can be achieved by adjusting the ratio of high-density polyethylene/low-density polyethylene.
Material chemical resistance: High-density polyethylene has better chemical resistance than low-density polyethylene.
Weather resistance of materials: To control the short-term or long-term performance of the hose, factors such as appearance, pressure resistance/drop resistance, sealing strength, environmental stress cracking resistance (ESCR value), fragrance and loss of active ingredients need to be considered.
Selection of masterbatch: Masterbatch plays an important role in the quality control of the hose. Therefore, when selecting masterbatch, the user company should consider whether it has good dispersibility, filtration and thermal stability, weather resistance and product resistance. Among them, the product resistance of the masterbatch is particularly important during the use of the hose. If the masterbatch is incompatible with the product, the color of the masterbatch will migrate to the product, and the consequences are very serious. Therefore, daily chemical companies should test the stability of new products and hoses (accelerated tests under specified conditions).
Types of varnish and their respective characteristics: The varnish used in the hose is divided into UV type and heat drying type, and can be divided into bright surface and matte surface in terms of appearance. Varnish not only provides beautiful visual effects, but also protects the contents and has a certain effect of blocking oxygen, water vapor and fragrance. Generally speaking, heat-drying varnish has good adhesion to subsequent hot stamping and silk-screen printing, while UV varnish has better gloss. Daily chemical companies can choose appropriate varnish according to the characteristics of their products. In addition, the cured varnish should have good adhesion, a smooth surface without pitting, folding resistance, wear resistance, corrosion resistance, and no discoloration during storage.
Requirements for the tube body/tube head: 1. The surface of the tube body should be smooth, without streaks, scratches, strains, or shrinkage deformation. The tube body should be straight and not bent. The tube wall thickness should be uniform. The tube wall thickness, tube length, and diameter tolerances should be within the specified range;
2. The tube head and tube body of the hose should be firmly connected, the connection line should be neat and beautiful, and the width should be uniform. The tube head should not be skewed after connection; 3. The tube head and the tube cover should match well, screw in and out smoothly, and there should be no slipping within the specified torque range, and there should be no water or air leakage between the tube and the cover;
Printing requirements: Hose processing usually uses lithographic offset printing (OFFSET), and most of the ink used is UV-dried, which usually requires strong adhesion and resistance to discoloration. The printing color should be within the specified depth range, the overprint position should be accurate, the deviation should be within 0.2mm, and the font should be complete and clear.
Requirements for plastic caps: Plastic caps are usually made of polypropylene (PP) injection molding. High-quality plastic caps should have no obvious shrinkage lines and flashing, smooth mold lines, accurate dimensions, and smooth fit with the tube head. They should not cause structural damage such as brittle cracks or cracks during normal use. For example, when the opening force is within the range, the flip cap should be able to withstand more than 300 folds without breaking.
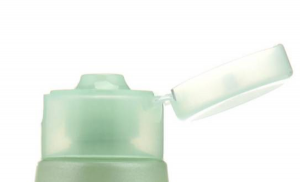
I believe that starting from the above aspects, the majority of daily chemical companies should be able to select high-quality hose packaging products.
Post time: Sep-06-2024