Color boxes account for the largest proportion of the cost of cosmetic packaging materials. At the same time, the process of color boxes is also the most complicated of all cosmetic packaging materials. Compared with plastic product factories, the equipment cost of color box factories is also very high. Therefore, the threshold of color box factories is relatively high. In this article, we briefly describe the basic knowledge of color box packaging materials.
Product Definition
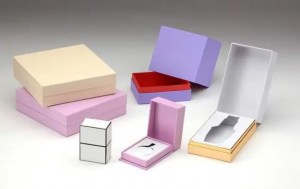
Color boxes refer to folding boxes and micro corrugated boxes made of cardboard and micro corrugated cardboard. In the concept of modern packaging, color boxes have changed from protecting products to promoting products. Consumers can judge the quality of products by the quality of color boxes.
Manufacturing process
The color box manufacturing process is divided into pre-press service and post-press service. Pre-press technology refers to the process involved before printing, mainly including computer graphic design and desktop publishing. Such as graphic design, packaging development, digital proofing, traditional proofing, computer cutting, etc. Post-press service is more about product processing, such as surface treatment (oiling, UV, lamination, hot stamping/silver, embossing, etc.), thickness processing (mounting corrugated paper), beer cutting (cutting finished products), color box molding, book binding (folding, stapling, glue binding).
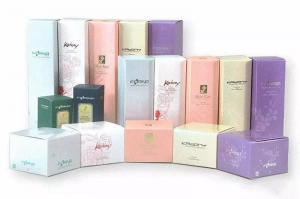
1. Manufacturing process
A. Designing film
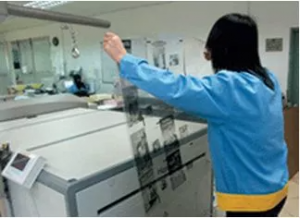
The art designer draws and typesets the packaging and printing documents, and completes the selection of packaging materials.
B. Printing
After getting the film (CTP plate), the printing is determined according to the film size, paper thickness, and printing color. From a technical point of view, printing is a general term for plate making (copying the original into a printing plate), printing (the graphic information on the printing plate is transferred to the surface of the substrate), and post-press processing (processing the printed product according to requirements and performance, such as processing into a book or box, etc.).
C. Making knife molds and mounting pits
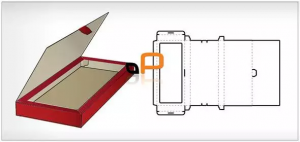
The production of the die needs to be determined according to the sample and the semi-finished product printed.
D. Appearance processing of printed products
Beautify the surface, including lamination, hot stamping, UV, oiling, etc.
E. Die-cutting
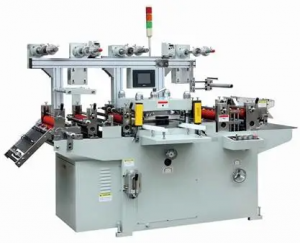
Use a beer machine + die cutter to die-cut the color box to form the basic style of the color box.
F. Gift box/sticky box
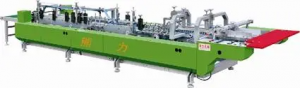
According to the sample or design style, glue the parts of the color box that need to be fixed and connected together, which can be glued by machine or by hand.
2. Common post-printing processes
Oil-coating process
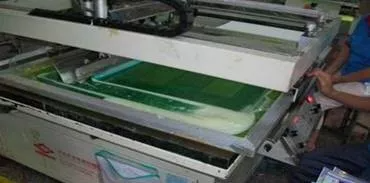
Oiling is a process of applying a layer of oil on the surface of the printed sheet and then drying it through a heating device. There are two methods, one is to use an oiling machine to oil, and the other is to use a printing press to print oil. The main function is to protect the ink from falling off and enhance the glossiness. It is used for ordinary products with low requirements.
Polishing process
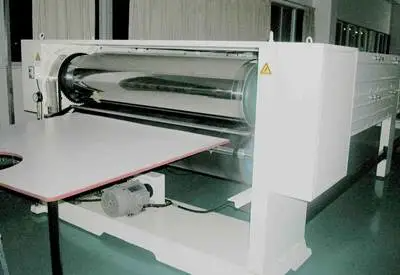
The printed sheet is coated with a layer of oil and then passed through a polishing machine, which is flattened by high temperature, light belt and pressure. It plays a smoothing role to change the surface of the paper, making it present a glossy physical property, and can effectively prevent the printed color from fading.
UV process
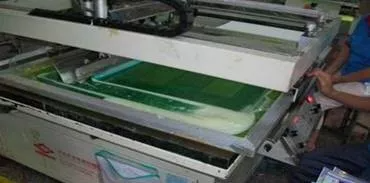
UV technology is a post-printing process that solidifies the printed matter into a film by applying a layer of UV oil on the printed matter and then irradiating it with ultraviolet light. There are two methods: one is full-plate UV and the other is partial UV. The product can achieve waterproof, wear-resistant and bright effects
Laminating process
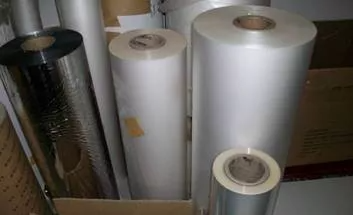
Lamination is a process in which glue is applied to the PP film, dried by a heating device, and then pressed on the printed sheet. There are two types of lamination, glossy and matte. The surface of the printed product will be smoother, brighter, more stain-resistant, water-resistant, and wear-resistant, with brighter colors and less prone to damage, which protects the appearance of various printed products and increases their service life.
Holographic transfer process
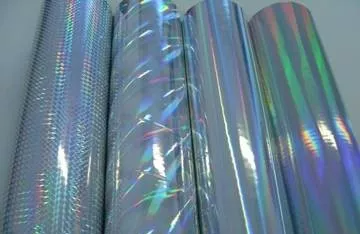
Holographic transfer uses a molding process to pre-press on a specific PET film and vacuum coat it, and then transfer the pattern and color on the coating to the paper surface. It forms an anti-counterfeiting and bright surface, which can improve the grade of the product.
Gold stamping process
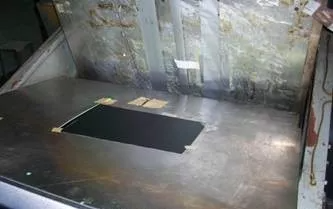
A special post-printing process that uses hot stamping (gilding) equipment to transfer the color layer on anodized aluminum foil or other pigment foil to the printed product under heat and pressure. There are many colors of anodized aluminum foil, with gold, silver, and laser being the most common. Gold and silver are further divided into glossy gold, matte gold, glossy silver, and matte silver. Gilding can improve the grade of the product
Embossed process
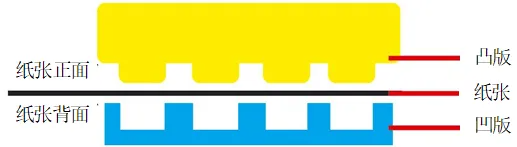
It is necessary to make one gravure plate and one relief plate, and the two plates must have good matching accuracy. The gravure plate is also called the negative plate. The concave and convex parts of the image and text processed on the plate are in the same direction as the processed product. The embossing process can improve the grade of the product
Paper mounting process
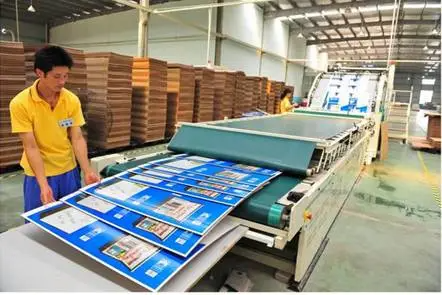
The process of applying glue evenly to two or more layers of corrugated cardboard, pressing and pasting them into cardboard that meets packaging requirements is called paper lamination. It increases the firmness and strength of the product to better protect the product.
Product Structure
1. Material classification
Facial tissue
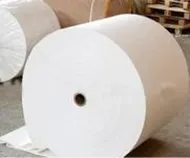
Facial paper mainly refers to coated paper, gorgeous card, gold card, platinum card, silver card, laser card, etc., which are the printable parts attached to the surface of corrugated paper. Coated paper, also known as coated printing paper, is generally used for facial paper. It is a high-grade printing paper made of base paper coated with white coating; the characteristics are that the paper surface is very smooth and flat, with high smoothness and good gloss. Coated paper is divided into single-sided coated paper, double-sided coated paper, matte coated paper, and cloth-textured coated paper. According to the quality, it is divided into three grades: A, B, and C. The surface of double-coated paper is smoother and glossier, and it looks more upscale and artistic. Common double-coated papers are 105G, 128G, 157G, 200G, 250G, etc.
Corrugated paper
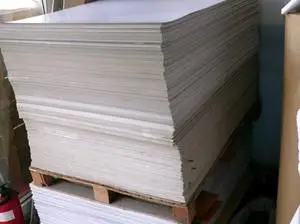
Corrugated paper mainly includes white board paper, yellow board paper, boxboard paper (or hemp board paper), offset board paper, letterpress paper, etc. The difference lies in the paper weight, paper thickness and paper stiffness. Corrugated paper has 4 layers: surface layer (high whiteness), lining layer (separating the surface layer and the core layer), core layer (filling to increase the thickness of the cardboard and improve the stiffness), bottom layer (cardboard appearance and strength). Conventional cardboard weight: 230, 250, 300, 350, 400, 450, 500g/㎡, conventional specifications of cardboard (flat): regular size 787*1092mm and large size 889*1194mm, conventional specifications of cardboard (roll): 26"28"31"33"35"36"38"40" etc. (suitable for printing), the printed surface paper is laminated on the corrugated paper to enhance the stiffness for shaping.
Cardboard
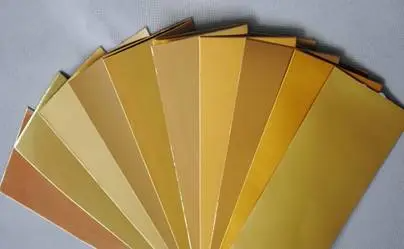
Generally, there are white cardboard, black cardboard, etc., with a gram weight ranging from 250-400g; folded and placed in a paper box for assembly and supporting products. The biggest difference between white cardboard and white board paper is that white board paper is made of mixed wood, while white cardboard is made of log pulp, and the price is more expensive than white board paper. The whole page of cardboard is cut by a die, and then folded into the required shape and placed inside the paper box to better protect the product.
2. Color box structure
A. Folding paper box
Made of folding-resistant paperboard with a thickness of 0.3-1.1mm, it can be folded and stacked in a flat shape for transportation and storage before shipping the goods. The advantages are low cost, small space occupation, high production efficiency, and many structural changes; the disadvantages are low strength, unsightly appearance and texture, and it is not suitable for packaging of expensive gifts.
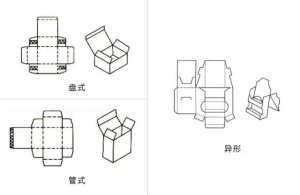
Disc type: the box cover is located on the largest box surface, which can be divided into cover, swing cover, latch type, positive press seal type, drawer type, etc.
Tube type: the box cover is located on the smallest box surface, which can be divided into insert type, lock type, latch type, positive press seal type, adhesive seal, visible open mark cover, etc.
Others: tube disc type and other special-shaped folding paper boxes
B. Paste (fixed) paper box
The base cardboard is glued and mounted with veneer material to form a shape, and it cannot be folded into a flat package after forming. The advantages are that many varieties of veneer materials can be selected, the anti-puncture protection is good, the stacking strength is high, and it is suitable for high-end gift boxes. The disadvantages are high production cost, cannot be folded and stacked, the veneer material is generally manually positioned, the printing surface is easy to be cheap, the production speed is low, and the storage and transportation are difficult
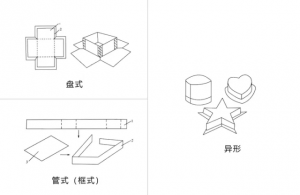
Disc type: The base box body and the bottom of the box are formed with one page of paper. The advantage is that the bottom structure is firm, and the disadvantage is that the seams on the four sides are prone to cracking and need to be reinforced.
Tube type (frame type): The advantage is that the structure is simple and easy to produce; the disadvantage is that the bottom plate is easy to fall off under pressure, and the seams between the frame adhesive surface and the bottom adhesive paper are clearly visible, affecting the appearance.
Combination type: tube disc type and other special-shaped folding paper boxes.
3. Color box structure case
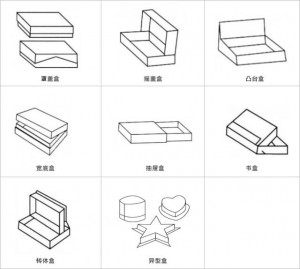
Cosmetics Application
Among cosmetic products, flower boxes, gift boxes, etc., all belong to the color box category.
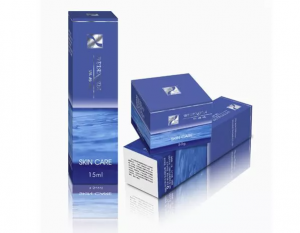
Purchasing considerations
1. Quotation method for color boxes
Color boxes are composed of multiple processes, but the approximate cost structure is as follows: face paper cost, corrugated paper cost, film, PS plate, printing, surface treatment, rolling, mounting, die cutting, pasting, 5% loss, tax, profit, etc.
2. Common problems
The quality problems of printing include color difference, dirt, graphic errors, lamination calendering, embossing, etc.; the quality problems of die cutting are mainly cracked lines, rough edges, etc.; and the quality problems of pasting boxes are debonding, overflowing glue, folding box forming, etc.
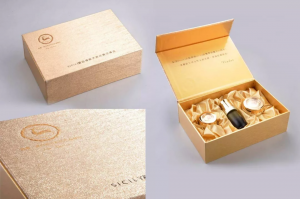
Post time: Nov-26-2024