Plastic bottle embryo is the initial form in the plastic bottle manufacturing process. Its parameters such as size, thread and weight are crucial and directly related to the use and performance of the bottle.
1. Relationship between preform quality and PET material quality
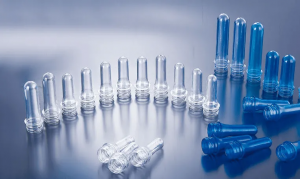
Polyethylene terephthalate (PET) is referred to as polyester. The production of PET plastic bottles can be divided into injection stretch blow molding (abbreviated as injection stretch blow molding) and extrusion stretch blow molding (abbreviated as extrusion stretch blow molding) according to the different preforms. Of the two molding methods, the injection stretch blow molding process is easy to control, has high production efficiency, and has less waste, and is more common.
When preparing blow-molded bottles, PET slices are first injected into the preform. It requires that the proportion of secondary recycled materials should not be too high (less than 5%), the number of recycling times should not exceed two times, and the molecular weight and viscosity should not be too low (molecular weight 31000-50000, intrinsic viscosity 0.78-0.85 cm3/g). According to the National Food Safety Law, the use of secondary recycled materials for food and drug packaging is prohibited. Injection molded preforms need to be stored for more than 24 hours before use. Unused preforms after heating must be stored for more than 48 hours before they can be heated again. The storage time of the bottle should not exceed six months.
The quality of the preform depends largely on the quality of the PET material, so it is necessary to choose materials that are easy to inflate and form, and formulate a reasonable preform forming process. Experiments show that PET preforms of the same viscosity are easier to blow mold with imported raw materials than with domestic raw materials. However, the same batch of preforms may have different blow molding processes with different production dates. The quality of the preform determines the difficulty of the blow molding process. The requirements for the preform are purity, transparency, no impurities, no color, appropriate injection point length, and halo around.
The heating of the preform is completed by a heating oven, and its temperature is set manually and adjusted automatically. In the oven, far-infrared lamps emit far-infrared rays to radiate heat to the preforms, and the fan at the bottom of the oven performs heat circulation to make the temperature in the oven uniform. The preforms rotate while moving forward in the oven, so that the wall of the preform is heated evenly.
The arrangement of the lamps in the oven is generally in the shape of a "zone" from top to bottom, with more at the two ends and less in the middle. The heat of the oven is controlled by the number of lamps turned on, the overall temperature setting, the oven power and the heating ratio of each section. The opening of the lamp tube should be adjusted in combination with the pre-blowing of the bottle. In order to make the oven work better, the adjustment of its height, cooling plate, etc. is very important. If the adjustment is improper, defects such as bulging bottle mouth (bottle mouth becomes larger) and hard neck (neck material cannot be pulled open) are prone to occur during blow molding.
2. Key factors in the design of bottle embryos
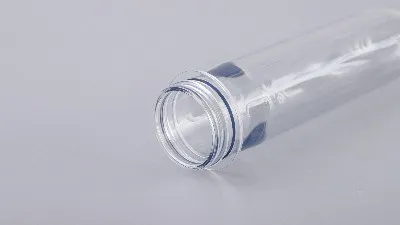
Plastic preforms are the initial form of plastic bottles in the manufacturing process. Their parameters such as size, thread and weight are crucial and directly related to the purpose and performance of the bottle.
First, the size of the preform is crucial to the final packaging container. When determining the size of the preform, we must first consider the purpose of the bottle. Is it for food, beverages, cosmetics or other fields? Different uses may require bottles of different shapes and capacities. By carefully considering the capacity requirements of the product, the capacity of the preform can be determined and the appropriate shape can be selected, such as round, square or oval.
Secondly, the thread (caliber) refers to the diameter of the bottle mouth and is also a key parameter. Measuring the thread ensures that the measurement is horizontal to obtain the accurate caliber size. The size of the thread directly affects the filling and pouring effect of the bottle. Different products may require different sizes of threads, so when designing a bottle, a reasonable choice of thread is necessary.
Finally, the gram weight of the preform refers to the weight of the bottle, including the bottle body and the bottle mouth. The gram weight of the bottle can be accurately measured by weighing or using a spiral scale. The determination of gram weight is directly related to the strength and durability of the bottle. When considering weight, it is necessary to balance the structural strength of the bottle and the material cost to ensure that the final product has both sufficient strength and meets the requirements of economy.
Overall, the size, thread and weight of the preform are important considerations in the design stage of the plastic bottle. Through careful measurement and reasonable selection, it can be ensured that the final bottle meets product requirements and industry standards and provides excellent packaging performance. During the bottle manufacturing process, continuous attention to the control of these parameters will help produce high-quality plastic bottles.
Post time: Mar-27-2025