Definition of Quality Product Standard
1. Applicable Objects
The content of this article is applicable to the quality inspection of various mask bags (aluminum film bags) packaging materials.
2. Terms and Definitions
Primary and secondary surfaces: The appearance of the product should be evaluated according to the importance of the surface under normal use;
Primary surface: The exposed part that is concerned after the overall combination. Such as the top, middle and visually obvious parts of the product.
Secondary surface: The hidden part and the exposed part that is not concerned or difficult to find after the overall combination. Such as the bottom of the product.
3. Quality defect level
Fatal defect: Violation of relevant laws and regulations, or causing harm to the human body during production, transportation, sales and use.
Serious defect: Involving functional quality and safety affected by structural quality, directly affecting the sales of the product or making the sold product fail to achieve the expected effect, and consumers will feel uncomfortable when using it.
General defect: Involving appearance quality, but does not affect the product structure and functional experience, and will not have a major impact on the appearance of the product, but makes consumers feel uncomfortable when using it.
Appearance quality requirements
1. Appearance requirements
Visual inspection shows no obvious wrinkles or creases, no perforations, ruptures, or adhesions, and the film bag is clean and free of foreign matter or stains.
2. Printing requirements
Color deviation: The main color of the film bag is consistent with the color standard sample confirmed by both parties and is within the deviation limit; there shall be no obvious color difference between the same batch or two consecutive batches. Inspection shall be carried out according to SOP-QM-B001.
Printing defects: Visual inspection shows no defects such as ghosting, virtual characters, blur, missing prints, knife lines, heterochromatic pollution, color spots, white spots, impurities, etc.
Overprint deviation: Measured with a steel ruler with an accuracy of 0.5mm, the main part is ≤0.3mm, and other parts are ≤0.5mm.
Pattern position deviation: Measured with a steel ruler with an accuracy of 0.5mm, the deviation shall not exceed ±2mm.
Barcode or QR code: The recognition rate is above Class C.
3. Hygiene requirements
The main viewing surface should be free of obvious ink stains and foreign color pollution, and the non-main viewing surface should be free of obvious foreign color pollution, ink stains, and the external surface should be removable.
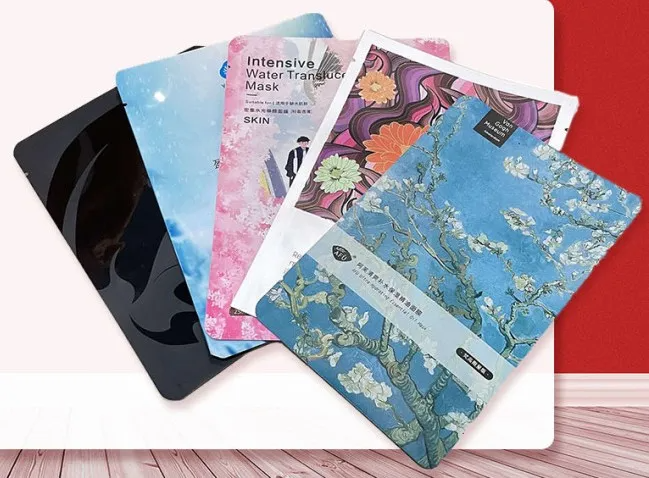
Structural quality requirements
Length, width and edge width: Measure the dimensions with a film ruler, and the positive and negative deviation of the length dimension is ≤1mm
Thickness: Measured with a screw micrometer with an accuracy of 0.001mm, the total thickness of the sum of the layers of material and the deviation from the standard sample shall not exceed ±8%.
Material: Subject to the signed sample
Wrinkle resistance: Push-pull method test, no obvious peeling between layers (composite film/bag)
Functional quality requirements
1. Cold resistance test
Take two mask bags, fill them with 30ml mask liquid, and seal them. Store one at room temperature and away from light as a control, and place the other in a -10℃ refrigerator. Take it out after 7 days and restore it to room temperature. Compared with the control, there should be no obvious difference (fading, damage, deformation).
2. Heat resistance test
Take two mask bags, fill them with 30ml mask liquid, and seal them. Store one at room temperature and away from light as a control, and place the other in a 50℃ constant temperature box. Take it out after 7 days and restore it to room temperature. Compared with the control, there should be no obvious difference (fading, damage, deformation).
3. Light resistance test
Take two mask bags, fill them with 30ml mask liquid, and seal them. Store one at room temperature and away from light as a control, and place the other in a light aging test box. Take it out after 7 days. Compared with the control, there should be no obvious difference (fading, damage, deformation).
4. Pressure resistance
Fill with water of the same weight as the net content, keep it under 200N pressure for 10 minutes, no cracks or leakage.
5. Sealing
Fill with water of the same weight as the net content, keep it under -0.06mPa vacuum for 1 minute, no leakage.
6. Heat resistance
Top seal ≥60 (N/15mm); side seal ≥65 (N/15mm). Tested according to QB/T 2358.
Tensile strength ≥50 (N/15mm); breaking force ≥50N; elongation at break ≥77%. Tested according to GB/T 1040.3.
7. Interlayer peel strength
BOPP/AL: ≥0.5 (N/15mm); AL/PE: ≥2.5 (N/15mm). Tested according to GB/T 8808.
8. Friction coefficient (inside/outside)
us≤0.2; ud≤0.2. Tested according to GB/T 10006.
9. Water vapor transmission rate (24h)
≤0.1(g/m2). Tested according to GB/T 1037.
10. Oxygen transmission rate (24h)
≤0.1(cc/m2). Tested according to GB/T 1038.
11. Solvent residue
≤10mg/m2. Tested according to GB/T 10004.
12. Microbiological indicators
Each batch of mask bags must have an irradiation certificate from the irradiation center. Mask bags (including mask cloth and pearlescent film) after irradiation sterilization: total bacterial colony count ≤10CFU/g; total mold and yeast count ≤10CFU/g.
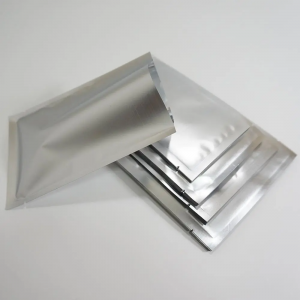
Acceptance method reference
1. Visual inspection: Appearance, shape, and material inspection are mainly visual inspection. Under natural light or 40W incandescent lamp conditions, the product is 30-40cm away from the product, with normal vision, and the surface defects of the product are observed for 3-5 seconds (except for printed copy verification)
2. Color inspection: The inspected samples and standard products are placed under natural light or 40W incandescent light or standard light source, 30cm away from the sample, with a 90º angle light source and a 45º angle line of sight, and the color is compared with the standard product.
3. Odor: In an environment without odor around, the inspection is carried out by smell.
4. Size: Measure the size with a film ruler with reference to the standard sample.
5. Weight: Weigh with a balance with a calibration value of 0.1g and record the value.
6. Thickness: Measure with a vernier caliper or micrometer with an accuracy of 0.02mm with reference to the standard sample and standard.
7. Cold resistance, heat resistance and light resistance test: Test the mask bag, mask cloth and pearlescent film together.
8. Microbiological index: Take the mask bag (containing mask cloth and pearlescent film) after irradiation sterilization, put in sterile saline with the same weight as the net content, knead the mask bag and the mask cloth inside, so that the mask cloth absorbs water repeatedly, and test the total number of bacterial colonies, molds and yeasts.
Packaging/Logistics/Storage
The product name, capacity, manufacturer name, production date, quantity, inspector code and other information should be marked on the packaging box. At the same time, the packaging carton must not be dirty or damaged and lined with a plastic protective bag. The box should be sealed with tape in the shape of an "I". The product must be accompanied by a factory inspection report before leaving the factory.
Post time: Dec-16-2024