The surface treatment process of cosmetic packaging products is the result of effective integration of color, coating, process, equipment, etc. Different processes create different effects of finished packaging products.
Ⅰ. About spraying
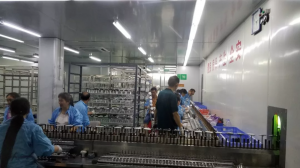
1. Spraying is the most common surface treatment, applicable to both plastic and hardware. Spraying generally includes oil spraying, powder spraying, etc., and the most common one is oil spraying. Sprayed coatings are commonly known as paints, which are composed of resins, pigments, solvents, and other additives. Plastic spraying generally has two coats of paint, the one with color on the surface is called topcoat, and the most transparent layer on the surface is called protective paint.
2. Introduction to the spraying process:
1) Preliminary cleaning. Such as electrostatic dust removal.
2) Spraying topcoat. The topcoat is generally the color that can be seen on the surface.
3) Drying topcoat. It is divided into natural drying at room temperature and special oven drying.
4) Cooling topcoat. Special oven drying requires cooling.
5) Spraying protective paint. Protective paint is generally used to protect the topcoat, most of which are transparent paints.
6) Curing protective paint.
7) QC inspection. Check whether it meets the requirements.
3. Rubber oil
Rubber oil, also known as elastic paint, hand-feel paint, is a two-component high-elastic hand-feel paint. The product sprayed with this paint has a special soft touch and high elastic surface feel. The disadvantages of rubber oil are high cost, general durability, and easy to fall off after long-term use. Rubber oil is widely used in communication products, audio-visual products, MP3, mobile phone shells, decorations, leisure and entertainment products, game console handles, beauty equipment, etc.
4. UV paint
1) UV paint is the English abbreviation of ultraviolet rays (Ultra-VioletRay). The commonly used UV wavelength range is 200-450nm. UV paint can only be cured under ultraviolet light.
2) Characteristics of UV paint: transparent and bright, high hardness, fast fixing speed, high production efficiency, protective topcoat, hardening and brightening the surface.
Ⅱ. About water plating
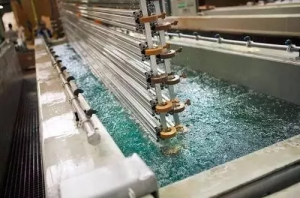
1. Water plating is an electrochemical process. In layman's terms, it is a surface processing method that immerses the product parts that need to be electroplated in an electrolyte, passes an electric current, and deposits metal on the surface of the parts by electrolysis to form a uniform, dense, and well-bonded metal layer.
2. Materials suitable for water plating: The most common is ABS, preferably electroplating grade ABS. Other common plastics such as PP, PC, PE, etc. are difficult to water plate.
Common surface colors: gold, silver, black, gun color.
Common electroplating effects: high gloss, matte, matte, mixed, etc.
Ⅲ. About vacuum plating
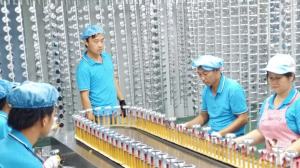
1. Vacuum plating is a type of electroplating. It is a method of plating a thin layer of metal plating on the surface of the product in a highly vacuum device.
2. The process flow of vacuum plating: surface cleaning-antistatic-primer spraying-primer baking-vacuum coating-topcoat spraying-topcoat baking-quality inspection-packaging.
3. Advantages and disadvantages of vacuum plating:
1) There are many plastic materials that can be electroplated.
2) It can be color-plated with rich colors.
3) The properties of plastics are not changed during electroplating, and local electroplating is convenient.
4) No waste liquid is generated, which is environmentally friendly.
5) Non-conductive vacuum plating can be performed.
6) The electroplating effect is brighter and brighter than water plating.
7) The productivity of vacuum plating is higher than that of water plating.
Its disadvantages are as follows:
1) The defective rate of vacuum plating is higher than that of water plating.
2) The price of vacuum plating is higher than that of water plating.
3) The surface of vacuum coating is not wear-resistant and needs UV protection, while water plating generally does not require UV protection.
Ⅳ. About IMD/In-Mold Decoration Technology
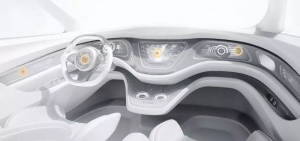
1. IMD's Chinese name: In-Mold Decoration Technology, also known as coating-free technology. English name: In-Mold Decoration, IMD is an internationally popular surface decoration technology, with a hardened transparent film on the surface, a printed pattern layer in the middle, a back injection layer, and ink in the middle, which can make the product resistant to friction, prevent the surface from being scratched, and keep the color bright for a long time and not easy to fade.
IMD in-mold decoration is a relatively new automated production process. Compared with traditional processes, IMD can simplify production steps and reduce disassembly components, so it can produce quickly and save time and cost. It also has the advantages of improving quality, increasing image complexity and improving product durability. IMD is currently the most efficient method. It is to print, high-pressure molding, punching on the surface of the film, and finally combine with plastic to form, eliminating secondary operation procedures and manpower hours. Especially when backlighting, multiple curved surfaces, imitation metal, hairline processing, logical light patterns, rib interference, etc., which cannot be handled by printing and painting processes, it is the time to use the IMD process.
IMD in-mold decoration can replace many traditional processes, such as thermal transfer, spraying, printing, electroplating and other appearance decoration methods. Especially for products that require multiple color images, backlights, etc.
Of course, it should be noted here: not all plastic surface decorations can be replaced by IMD technology. IMD still has material technology bottlenecks (such as the inverse relationship between hardness and stretching, positioning accuracy, spacing between special shapes and bumps, draft angle, etc.) Specific products must provide 3D drawings for professional engineers to analyze.
2. IMD includes IML, IMF, and IMR
IML: IN MOLDING LABEL (a technique that places the printed and punched decorative sheet into the injection mold, and then injects the resin into the ink layer on the back of the molded sheet to make the resin and the sheet bonded into one solidified shape. Printing → punching → internal plastic injection.) (No stretching, small curved surface, used for 2D products);
IMF: IN MOLDING FILM (roughly the same as IML but mainly used for 3D processing based on IML. Printing → molding → punching → internal plastic injection. Note: molding is mostly PC vacuum\high pressure molding.) (suitable for high-stretch products, 3D products);
IMR: IN MOLDING ROLLER (the focus is on the release layer on the rubber. PET FILM → printing release agent → printing ink → printing adhesive → internal plastic injection → ink and plastic bonding → after opening the mold, the rubber will automatically release from the ink. Japan calls it thermal transfer or thermal transfer. This machine uses ROLL TOROLL method, and the alignment is operated by CCD computer. His sheet customization cycle is relatively long, the mold cost is relatively high, the technology is not exported, only the Japanese side has it. ) (The film on the surface of the product is removed, leaving only the ink on the surface of the product.);
3. The difference between IML, IMF and IMR (whether a thin film is left on the surface).
Advantages of IMD products:
1) Scratch resistance, strong corrosion resistance, and long service life.
2) Good three-dimensional sense.
3) Dustproof, moisture-proof, and strong anti-deformation ability.
4) The color can be changed at will, and the pattern can be changed at will.
5) The pattern is accurately positioned.
V. About silk screen printing
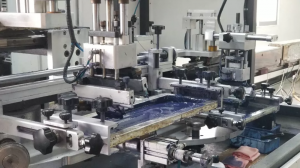
1. Silk screen printing is an ancient but widely used printing method.
1) Use a scraper to apply ink on the screen.
2) Use a scraper at a fixed angle to evenly scrape the ink to one side. At this time, the ink will be printed on the printed object due to penetration according to the pattern when the screen was manufactured, and it can be printed repeatedly.
3) The printed screen can be kept and used after washing.
2. Places where silk screen printing is applied: paper printing, plastic printing, wood product printing, glass, ceramic product printing, leather product printing, etc.
Ⅵ. About pad printing
1. Pad printing is one of the special printing methods. It can print text, graphics and images on the surface of irregular objects, and is now becoming an important special printing. For example, the text and patterns on the surface of mobile phones are printed in this way, and the surface printing of many electronic products such as computer keyboards, instruments, and meters are all completed by pad printing.
2. The pad printing process is very simple. It uses a steel (or copper, thermoplastic plastic) gravure and a curved pad printing head made of silicone rubber material. The ink on the gravure is dipped onto the surface of the pad printing head, and then pressed against the surface of the required object to print text, patterns, etc.
3. The difference between pad printing and silk screen printing:
1) Pad printing is suitable for irregular curved surfaces and curved surfaces with large arcs, while silk screen printing is suitable for flat surfaces and small curved surfaces.
2) Pad printing requires steel plates to be exposed, while silk screen printing uses screens.
3) Pad printing is transfer printing, while silk screen printing is direct leak printing.
4) The mechanical equipment used by the two is very different.
VII. About water transfer printing
1. Water transfer printing, commonly known as water decals, refers to the transfer of patterns and patterns on water-soluble films to substrates through water pressure.
2. Comparison between water transfer and IML:
IML process: accurate pattern position, arbitrary pattern edge wrapping (chamfer or undercut cannot be wrapped), variable pattern effect, and never fade.
Water transfer: inaccurate pattern position, limited pattern edge wrapping, limited pattern effect (special printing effect cannot be achieved), and will fade.
VIII. About thermal transfer
1. Thermal transfer is an emerging printing process that has been introduced from abroad for only more than 10 years. The printing method of this process is divided into two parts: transfer film printing and transfer processing. Transfer film printing adopts dot printing (resolution up to 300dpi), and the pattern is pre-printed on the surface of the film. The printed pattern is rich in layers, bright in color, ever-changing, with small color difference and good reproducibility. It can meet the requirements of the designer and is suitable for mass production; transfer processing uses a thermal transfer machine to process (heating and pressurizing) once to transfer the exquisite pattern on the transfer film to the product surface. After molding, the ink layer and the product surface are integrated, which is realistic and beautiful, greatly improving the grade of the product. However, due to the high technical content of the process, many materials need to be imported.
2. The thermal transfer process is applied to the surfaces of various products such as ABS, PP, plastic, wood, and coated metal. The thermal transfer film can be designed and produced according to customer requirements, and the pattern can be transferred to the surface of the workpiece through hot pressing to improve the product grade. The thermal transfer process is widely used in plastics, cosmetics, toys, electrical appliances, building materials, gifts, food packaging, stationery and other industries.
IX. About thermal sublimation dye printing
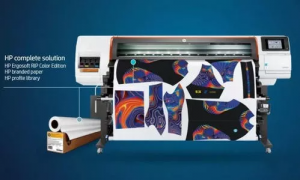
1. This method is specially created for the surface decoration of prefabricated products and three-dimensional plastic products. This method cannot provide scratch resistance and other protection for the product surface. On the contrary, it can provide a printing quality that is not easy to fade and can still show beautiful colors even if scratched. Unlike screen printing or painting, the color saturation presented by this method is much higher than other coloring methods.
2. The dye used in thermal sublimation can penetrate about 20-30 microns into the surface of the material, so even if the surface is scrubbed or scratched, its color can still be maintained very bright. This method is also widely used in various products, including SONY's laptop VAIO. This computer uses this method to make surface treatments of different colors and patterns, making this product more distinctive and personalized.
Ⅹ. About baking varnish
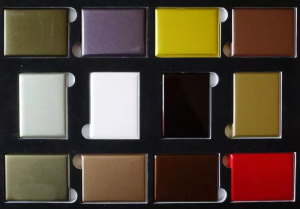
1. Baking varnish means that after spraying or painting, the workpiece is not allowed to cure naturally, but the workpiece is sent to the baking varnish room, and the paint layer is cured by electric heating or far infrared heating.
2. The difference between baking varnish and ordinary paint: After baking varnish, the paint layer is more compact, not easy to fall off, and the paint film is uniform and the color is full.
3. Piano lacquer process is a kind of baking varnish process. Its process is very complicated. First, putty needs to be applied on the wooden board as the bottom layer of spraying paint; after leveling the putty, wait for the putty to dry, and polish it smooth; then spray the primer 3-5 times repeatedly, and polish it with water sandpaper and grinding cloth after each spraying; finally, spray 1-3 times of glossy topcoat, and then use high temperature baking to cure the paint layer. The primer is a cured transparent paint with a thickness of about 0.5mm-1.5mm. Even if the iron cup temperature is 60-80 degrees, there will be no problem on its surface!
XI. About oxidation
1. Oxidation refers to the chemical reaction between an object and oxygen in the air, which is called oxidation reaction. It is a natural phenomenon. The oxidation described here refers to the surface treatment process of hardware products. It is an electro-oxidation reaction controlled by humans. Anodic oxidation is widely used.
2. Process flow: alkali washing--water washing-bleaching-water washing-activation-water washing-aluminum oxidation-water washing-dyeing-water washing-sealing-water washing-drying-quality inspection-warehousing.
3. The role of oxidation: protective and decorative, can be colored, insulated, improve the bonding strength with organic coatings, and improve the bonding strength with inorganic covering layers.
4. Secondary oxidation: The product is oxidized twice by blocking or deoxidizing the surface of the product, which is called secondary oxidation.
1) Different colors on the same product can be close or very different.
2) The production of the LOGO protruding on the surface of the product. The LOGO protruding on the surface of the product can be stamped or obtained through secondary oxidation.
XIⅠ. About mechanical wire drawing
1. Mechanical wire drawing is a process of rubbing marks on the surface of the product through mechanical processing. There are several types of mechanical wire drawing, such as straight lines, random lines, threads, corrugations, and sun lines.
2. Materials suitable for mechanical wire drawing:
1) Mechanical wire drawing belongs to the surface treatment process of hardware products.
2) Plastic products cannot be directly mechanically wire drawn. Plastic products after water plating can also be mechanically wire drawn to achieve lines, but the coating should not be too thin, otherwise it is easy to be broken.
3) Among metal materials, the most common mechanical wire drawing is aluminum and stainless steel. Since the surface hardness and strength of aluminum are lower than those of stainless steel, the mechanical wire drawing effect is better than stainless steel.
4) Other hardware products.
XIⅠⅠ. About laser engraving
1. Laser engraving, also known as laser engraving or laser marking, is a process of surface treatment using optical principles.
2. Application of laser engraving: Laser engraving is suitable for almost all materials, and hardware and plastics are common fields. In addition, there are bamboo and wood products, plexiglass, metal plates, glass, stone, crystal, Corian, paper, two-color plates, aluminum oxide, leather, plastic, epoxy resin, polyester resin, sprayed metal, etc.
3. The difference between laser wire drawing and mechanical wire drawing:
1) Mechanical wire drawing is to make textures by mechanical processing, while laser wire drawing is to burn out textures by laser light energy.
2) Relatively speaking, the texture of mechanical wire drawing is not very clear, while the texture of laser wire drawing is clear.
3) The surface of mechanical wire drawing has a sense of bumps and concavities when touched, while the surface of laser wire drawing has a sense of bumps and concavities when touched.
XIⅠⅡ.About high-gloss trimming
High-gloss trimming is to cut a circle of bright bevels on the edge of hardware products through a high-speed CNC machine.
1) It belongs to the surface treatment process of hardware products.
2) Among metal materials, aluminum is the most widely used for high-gloss cutting, because aluminum is relatively soft, has excellent cutting performance, and can obtain a very bright surface effect.
3) The processing cost is high, and it is generally used for edge cutting of metal parts.
4) It is widely used in mobile phones, electronic products, and digital products.
XⅤ. About Brushing
1. Brushing is a method of cutting patterns on the surface of a product through mechanical processing.
2. Brushing application places:
1) It belongs to the surface treatment process of hardware products.
2) Metal nameplates, the product labels or company logos on them have inclined or straight silk stripes.
3) Some patterns with obvious depth on the surface of hardware products.
XⅥ. About sandblasting
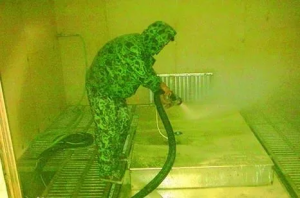
Sandblasting is a process of cleaning and roughening the surface of a substrate by the impact of high-speed sand flow. Compressed air is used as the power to form a high-speed jet beam to spray the material (copper ore sand, quartz sand, corundum, iron sand, Hainan sand) at high speed onto the surface of the workpiece to be processed, so that the appearance or shape of the outer surface of the workpiece surface changes. Due to the impact and cutting action of the abrasive on the workpiece surface, the surface of the workpiece obtains a certain degree of cleanliness and different roughness, and the mechanical properties of the workpiece surface are improved, thereby improving the fatigue resistance of the workpiece, increasing the adhesion between it and the coating, prolonging the durability of the coating, and also facilitating the leveling and decoration of the coating.
2. Application scope of sandblasting
1) Pretreatment of workpiece coating and bonding Sandblasting can remove all dirt such as rust on the surface of the workpiece, and establish a very important basic pattern (commonly known as the rough surface) on the surface of the workpiece, and can achieve different degrees of roughness by replacing abrasives of different particle sizes, greatly improving the bonding force between the workpiece and the coating and plating material. Or make the bonding parts more firmly bonded and of better quality.
2) Cleaning and polishing of rough surfaces of castings and workpieces after heat treatment Sandblasting can clean all dirt (such as scale, oil and other residues) on the surface of castings and forgings and workpieces after heat treatment, and polish the surface of the workpiece to improve the finish of the workpiece, so that the workpiece can show a uniform and consistent metal color, making the appearance of the workpiece more beautiful.
3) Burr cleaning and surface beautification of machined parts Sandblasting can clean the tiny burrs on the surface of the workpiece and make the surface of the workpiece smoother, eliminating the harm of burrs and improving the grade of the workpiece. In addition, sandblasting can create very small fillets at the junction of the workpiece surface, making the workpiece more beautiful and more precise.
4) Improve the mechanical properties of parts. After sandblasting, mechanical parts can produce uniform and fine concave and convex surfaces on the surface of the parts, so that lubricating oil can be stored, thereby improving lubrication conditions, reducing noise and increasing the service life of the machine.
5) Polishing effect For some special-purpose workpieces, sandblasting can achieve different reflections or matte at will. Such as polishing of stainless steel workpieces and plastics, polishing of jade, matte surface of wooden furniture, patterns on frosted glass surface, and roughening of fabric surface.
17. About corrosion
1. Corrosion is corrosion carving, which refers to the use of decorative materials to produce patterns or text on the metal surface.
2. Application of corrosion:
1) It belongs to the surface treatment process of hardware products.
2) Decorative surface, which can make some relatively delicate patterns and text on the metal surface.
3) Corrosion processing can produce tiny holes and grooves.
4) Mould etching and biting.
18. About polishing
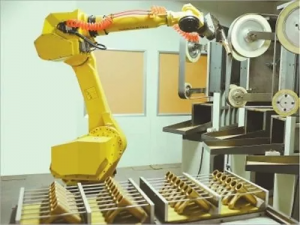
1. Polishing is the process of using other tools or methods to brighten the surface of a workpiece. The main purpose is to obtain a smooth surface or mirror gloss, and sometimes it is also used to eliminate gloss (matte).
2. Common polishing methods include: mechanical polishing, chemical polishing, electrolytic polishing, ultrasonic polishing, fluid polishing, and magnetic grinding polishing.
3. Polishing application places:
1) Generally speaking, all products that need a bright surface must be polished.
2) Plastic products are not polished directly, but the abrasive is polished.
19. About hot stamping
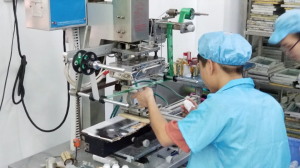
1. Hot stamping, commonly known as hot stamping, is a special printing process that does not use ink. The metal printing plate is heated, foil is applied, and golden text or patterns are embossed on the printed matter. With the rapid development of hot stamping foil and packaging industry, the application of electroplated aluminum hot stamping is becoming more and more extensive.
2. The hot stamping process uses the principle of hot pressing transfer to transfer the aluminum layer in electroplated aluminum to the surface of the substrate to form a special metal effect. Because the main material used for hot stamping is electroplated aluminum foil, hot stamping is also called electroplated aluminum hot stamping. Electroplated aluminum foil is usually composed of multiple layers of materials, the base material is often PE, followed by separation coating, color coating, metal coating (aluminum plating) and glue coating.
The basic hot stamping process is that under pressure, that is, when the electroplated aluminum is pressed by the hot stamping plate and the substrate, the hot-melt silicone resin layer and adhesive on the electroplated aluminum are melted by heat. At this time, the viscosity of the hot-melted silicone resin becomes smaller, and the viscosity of the special heat-sensitive adhesive increases after being melted by heat, so that the aluminum layer is peeled off from the electroplated aluminum base film and transferred to the substrate at the same time. With the removal of pressure, the adhesive quickly cools and solidifies, and the aluminum layer is firmly attached to the substrate, completing a hot stamping process.
3. Hot stamping has two main functions: one is surface decoration, which can increase the added value of the product. Hot stamping combined with other processing methods such as embossing technology can better show the strong decorative effect of the product: the second is to give the product a higher anti-counterfeiting performance, such as the use of holographic positioning hot stamping trademark logos. After hot stamping, the product has a clear and beautiful pattern, bright and eye-catching colors, wear resistance and weather resistance. At present, the hot stamping process on printed cigarette labels accounts for more than 85%. In graphic design, hot stamping can play a role in adding the finishing touch and highlighting the design theme. It is particularly suitable for the decoration of trademarks and registered names.
20. About flocking
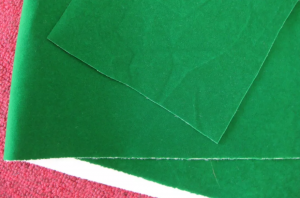
Flocking is often considered to be only for decoration, but in fact it has many advantages. For example, in jewelry boxes and cosmetics, flocking is needed to protect jewelry and cosmetics. It can also prevent condensation, so it is used in car interiors, boats, or air conditioning systems. The two most creative applications I can imagine are to flock ceramic tableware, and the other is Miele's vacuum cleaner.
21. About Out-of-Mold Decoration
Out-of-mold decoration is often regarded as an extension of injection molding, rather than another independent process. Covering the outer layer of a mobile phone with cloth seems to require exquisite craftsmanship to produce a special effect, but it can be produced quickly and beautifully through out-of-mold decoration. More importantly, it can be made directly on the mold without additional manual post-processing.
22. About Self-Healing Coating
1. This coating has a magical self-healing ability. When there are small scratches or fine lines on the surface, as long as it is hit by a heat source, the surface will repair the scars by itself. The principle is to use the increased fluidity of polymer materials in high temperature environments, so that after heating, they will flow towards scratches or dents due to increased fluidity and fill them. This surface treatment can provide unprecedented protection and durability.
It is very good for the protection of some cars, especially when we park the car under the sun, the coating on its surface will automatically repair small fine lines or scratches, presenting the most perfect surface.
2. Related applications: In addition to the protection of body panels, it may be used on the surface of buildings in the future?
23. About waterproof coating
1. Traditional waterproof coatings must be covered with a layer of film, which is not only unsightly, but also changes the surface properties of the object itself. The nano waterproof coating invented by P2I uses vacuum sputtering to attach a polymer waterproof coating to the surface of the workpiece in a closed space at room temperature. Since the thickness of this coating is in nanometers, it is almost unnoticeable in appearance. This method is applicable to various materials and geometric shapes. Even some objects with complex shapes and a combination of several materials can be successfully coated with a waterproof layer by P2I.
2. Related applications: This technology can provide waterproof functions for electronic products, clothing, shoes, etc. Zippers of clothes and joints of electronic products can be coated. Others, including laboratory precision instruments and medical equipment, must also have waterproof functions. For example, the dropper in the laboratory must have a water-repellent function to prevent liquid adhesion, so as to ensure that the amount of liquid in the experiment is accurate and lossless.
Post time: Apr-22-2025