In order to make the product more personalized, most of the formed packaging products need to be surface colored. There are various surface treatment processes for daily chemical packaging. Here we mainly introduce several common processes in the cosmetic packaging industry, such as vacuum coating, spraying, electroplating, anodizing, injection molding and color change.
1.Vacuum coating process definition
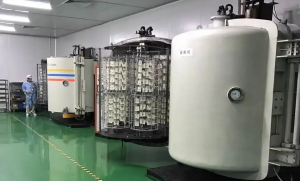
Vacuum coating mainly refers to a type of product that needs to be coated under a higher vacuum degree. The film substrate to be coated is placed in a vacuum evaporator, and a vacuum pump is used to evacuate the vacuum in the coating to 1.3×10-2~1.3×10-3Pa. The crucible is heated to melt and evaporate high-purity aluminum wire (purity 99.99%) at a temperature of 1200℃~1400℃ into gaseous aluminum. The gaseous aluminum particles are deposited on the surface of the moving film substrate, and after cooling and reduction, a continuous and bright metal aluminum layer is formed.
2.Vacuum coating process characteristics
Process cost: mold cost (none), unit cost (medium)
Suitable output: single piece to large batch
Quality: high quality, high brightness and product surface protective layer
Speed: medium production speed, 6 hours/cycle (including painting)
3.Composition of vacuum coating process system
1. Electroplating equipment
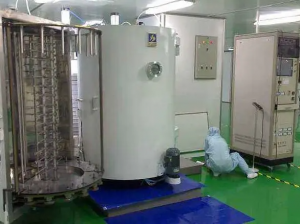
Vacuum plating is the most common metal surface treatment technology. Since no mold is required, the process cost is very low, and lifelike colors can also be applied in vacuum plating, so that the product surface can achieve the effect of anodized aluminum, bright chrome, gold, silver, copper and gunmetal (a copper-tin alloy). Vacuum plating can treat the surface of cheap materials (such as ABS) into the effect of metal surface at a low cost. The surface of the vacuum plated workpiece should be kept dry and smooth, otherwise it will greatly affect the surface effect.
2. Applicable materials
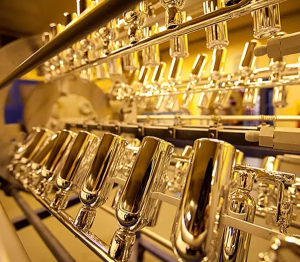
Metal materials can be gold, silver, copper, zinc, chromium, aluminum, etc., among which aluminum is the most commonly used. Plastic materials are also applicable, such as ABS, etc.
4.Process flow reference
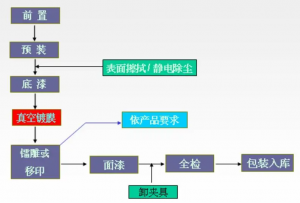
Let's take a plastic part as an example: spray a layer of primer on the workpiece first, and then do electroplating. Since the workpiece is a plastic part, air bubbles and organic gases will remain during injection molding, and moisture in the air will be absorbed when placed. In addition, since the plastic surface is not flat enough, the surface of the workpiece directly electroplated is not smooth, the gloss is low, the metal feel is poor, and there will be bubbles, blisters and other undesirable conditions. After spraying a layer of primer, a smooth and flat surface will be formed, and the bubbles and blisters existing in the plastic itself will be eliminated, so that the effect of electroplating can be displayed.
5.Application in the cosmetic packaging industry
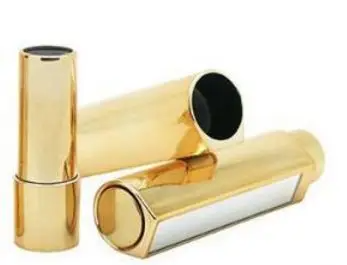
Vacuum coating has various applications in the cosmetic packaging industry, such as lipstick tube outer components, pump head outer components, glass bottles, bottle cap outer components, etc.
Post time: Feb-24-2025