Hot stamping is an important method of metal effect surface finishing. It can enhance the visual effect of trademarks, cartons, labels and other products. Hot stamping and cold stamping are both used to make product packaging bright and dazzling, which helps to grab customers' attention and attract consumers' attention.
Hot stamping/hot stamping
The essence of hot stamping is transfer printing, which is a process of transferring the pattern on the electroplated aluminum to the substrate through the action of heat and pressure. When the printing plate is heated to a certain degree along with the attached electric heating base plate, it is pressed against the paper through the electroplated aluminum film, and the glue layer, metal aluminum layer and color layer attached to the polyester film are transferred to the paper by the action of temperature and pressure.
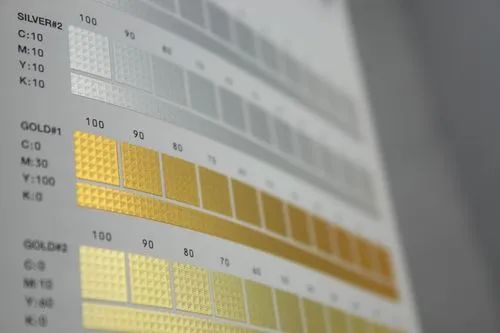
Hot stamping technology
Refers to the processing technology of transferring the hot stamping material (usually electroplated aluminum film or other special coating) to the hot stamping object through a specific hot stamping pattern on the hot stamping object such as paper, cardboard, fabric, coating, etc.
1. Classification
Hot stamping can be divided into automatic hot stamping and manual hot stamping according to the degree of automation of the process. According to the hot stamping method, it can be divided into the following four types:
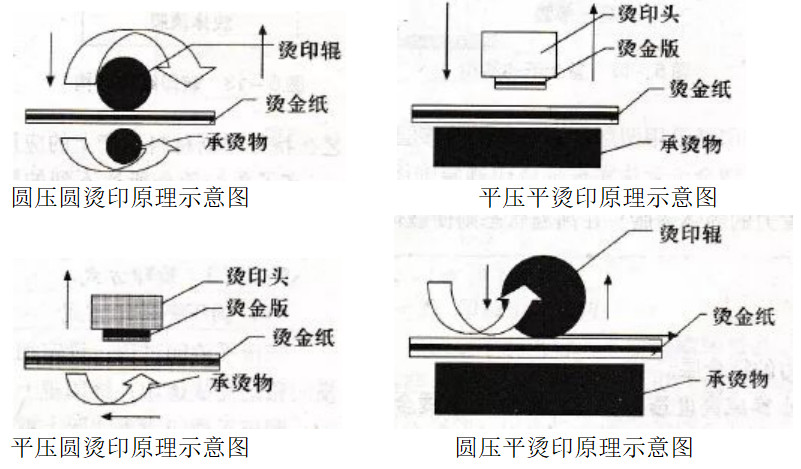
2. Advantages
1) Good quality, high precision, clear and sharp edges of hot stamping images.
2) High surface gloss, bright and smooth hot stamping patterns.
3) A wide range of hot stamping foils are available, such as different colors or different gloss effects, as well as hot stamping foils suitable for different substrates.
4) Three-dimensional hot stamping can be performed. It can give the packaging a unique touch. Moreover, the three-dimensional hot stamping plate is made by computer numerical control engraving (CNC) to make the hot stamping plate, so that the three-dimensional layers of the hot stamping image are obvious, forming a relief effect on the surface of the printed product, and producing a strong visual impact.
3. Disadvantages
1) Hot stamping process requires special equipment
2) Hot stamping process requires heating device
3) Hot stamping process requires heating device to make hot stamping plate Therefore, hot stamping can achieve high-quality hot stamping effect, but the cost is also higher. The price of rotary hot stamping roller is relatively high, accounting for a large part of the cost of hot stamping process.
4. Features
The pattern is clear and beautiful, the color is bright and eye-catching, wear-resistant and weather-resistant. On printed cigarette labels, the application of hot stamping technology accounts for more than 85%, and hot stamping in graphic design can play a role in adding the finishing touch and highlighting the design theme, especially for trademarks and registered names, the effect is more significant.
5. Influencing factors
Temperature
The electric heating temperature should be controlled between 70 and 180℃. For larger hot stamping areas, the electric heating temperature should be relatively higher; for small text and lines, the hot stamping area is smaller, the hot stamping temperature should be lower. At the same time, the hot stamping temperature suitable for various types of electroplated aluminum is also different. 1# is 80-95℃; 8# is 75-95℃; 12# is 75-90℃; 15# is 60-70℃; and pure gold foil is 80-130℃; gold powder foil and silver powder foil are 70-120℃. Of course, the ideal hot stamping temperature should be the lowest temperature that can emboss clear graphic lines, and it can only be determined through trial hot stamping.
Air pressure
The hot stamping transfer of the aluminum layer must be completed by pressure, and the size of the hot stamping pressure affects the adhesion of the electroplated aluminum. Even if the temperature is appropriate, if the pressure is insufficient, the electroplated aluminum cannot be transferred to the substrate well, which will cause problems such as weak imprints and flowery plates; on the contrary, if the pressure is too high, the compression deformation of the pad and the substrate is too large, the imprint will be coarse, and even sticky and paste the plate. Usually, the hot stamping pressure should be appropriately reduced to achieve no fading and good adhesion.
Adjusting the hot stamping pressure should be based on a variety of factors such as the substrate, hot stamping temperature, vehicle speed, and the electroplated aluminum itself. Generally speaking, the hot stamping pressure should be smaller when the paper is strong and smooth, the printed ink layer is thick, and the hot stamping temperature is high and the vehicle speed is slow. On the contrary, it should be larger. The hot stamping pressure must be uniform. If it is found that the hot stamping is not good and there are flowery patterns in a part, it is likely that the pressure here is too small. A layer of thin paper should be placed on the flat plate at that place to balance the pressure.
The hot stamping pad also has a greater impact on the pressure. Hard pads can make the prints beautiful and are suitable for strong and smooth paper, such as coated paper and glass cardboard; while soft pads are the opposite, and the prints are rough, which is suitable for hot stamping of large areas, especially for uneven surfaces, poor flatness and smoothness, and rougher paper. At the same time, the installation of hot stamping foil should not be too tight or too loose. If it is too tight, the writing will be missing strokes; if it is too loose, the writing will be unclear and the plate will be smudged.
Speed
Hot stamping speed actually reflects the contact time between the substrate and the hot stamping foil during hot stamping, which directly affects the fastness of hot stamping. If the hot stamping speed is too fast, it will cause the hot stamping to fail or the print to be blurred; if the hot stamping speed is too slow, it will affect both the hot stamping quality and production efficiency.
Cold foil technology
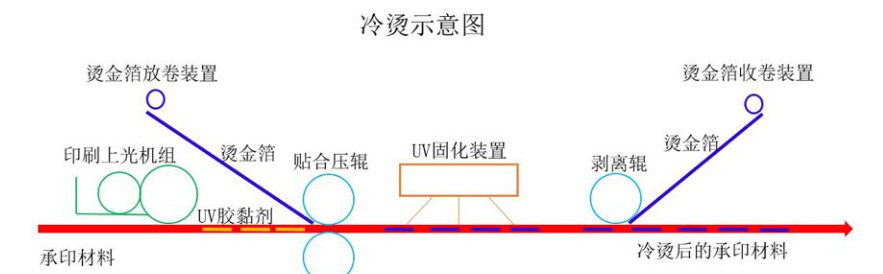
Cold stamping technology refers to the method of transferring hot stamping foil to the printing material using UV adhesive. The cold stamping process can be divided into dry lamination cold stamping and wet lamination cold stamping.
1. Process steps
Dry lamination cold stamping process
The coated UV adhesive is first cured before hot stamping. When cold stamping technology first came out, the dry lamination cold stamping process was used, and its main process steps are as follows:
1) Print cationic UV adhesive on the roll printing material.
2) Cure the UV adhesive.
3) Use a pressure roller to compound the cold stamping foil and the printing material.
4) Peel off the excess hot stamping foil from the printing material, leaving only the required hot stamping image and text on the part coated with the adhesive.
It is worth noting that when using the dry lamination cold stamping process, the UV adhesive should be cured quickly, but not completely. It is necessary to ensure that it still has a certain viscosity after curing so that it can be well bonded with the hot stamping foil.
Wet lamination cold stamping process
After applying the UV adhesive, hot stamping is performed first and then the UV adhesive is cured. The main process steps are as follows:
1) Printing free radical UV adhesive on the roll substrate.
2) Compounding cold stamping foil on the substrate.
3) Curing the free radical UV adhesive. Since the adhesive is sandwiched between the cold stamping foil and the substrate at this time, the UV light must pass through the hot stamping foil to reach the adhesive layer.
4) Peeling the hot stamping foil from the substrate and forming a hot stamping image on the substrate.
It should be noted that:
The wet lamination cold stamping process uses free radical UV adhesive to replace the traditional cationic UV adhesive;
The initial adhesion of the UV adhesive should be strong, and it should no longer be sticky after curing;
The aluminum layer of the hot stamping foil should have a certain light transmittance to ensure that the UV light can pass through and trigger the curing reaction of the UV adhesive.
The wet lamination cold stamping process can hot stamp metal foil or holographic foil on the printing press, and its application range is becoming wider and wider. At present, many narrow-width carton and label flexographic printing presses have this online cold stamping capability.
2. Advantages
1) No expensive special hot stamping equipment is required.
2) Ordinary flexographic plates can be used, and there is no need to make metal hot stamping plates. The plate making speed is fast, the cycle is short, and the production cost of the hot stamping plate is low.
3) The hot stamping speed is fast, up to 450fpm.
4) No heating device is required, saving energy.
5) Using a photosensitive resin plate, the halftone image and solid color block can be stamped at the same time, that is, the halftone image and solid color block to be stamped can be made on the same stamping plate. Of course, just like printing halftone and solid color blocks on the same printing plate, the stamping effect and quality of both may be lost to a certain extent.
6) The application range of the stamping substrate is wide, and it can also be stamped on heat-sensitive materials, plastic films, and in-mold labels.
3. Disadvantages
1) Stamping cost and process complexity: Cold stamping images and texts usually require lamination or glazing for secondary processing and protection.
2) The aesthetics of the product is relatively reduced: the applied high-viscosity adhesive has poor leveling and is not smooth, which causes diffuse reflection on the surface of the cold stamping foil, affecting the color and gloss of the stamping images and texts.
4. Application
1) Design flexibility (various graphics, multiple colors, multiple materials, multiple processes);
2) Fine patterns, hollow text, dots, large solids;
3) Gradient effect of metallic colors;
4) High precision of post-printing;
5) Flexible post-printing - offline or online;
6) No damage to the material of the substrate;
7) No deformation of the substrate surface (no temperature/pressure required);
8) No indentation on the back of the substrate, which is especially important for some printed products, such as magazines and book covers.
Post time: Aug-05-2024