ਥਰਮਲ ਟ੍ਰਾਂਸਫਰ ਟੈਕਨਾਲੋਜੀ ਦਾ ਸ਼ਿੰਗਾਰ ਪੈਕਿੰਗ ਸਮੱਗਰੀ ਦੇ ਸਤਹ ਦੇ ਇਲਾਜ ਵਿਚ ਇਕ ਆਮ ਪ੍ਰਕਿਰਿਆ ਹੈ. ਇਹ ਇਕ ਪ੍ਰਕਿਰਿਆ ਹੈ ਜੋ ਛਪਾਈ ਅਤੇ ਅਨੁਕੂਲਿਤ ਰੰਗਾਂ ਅਤੇ ਪੈਟਰਨ ਵਿਚ ਆਪਣੀ ਸਹੂਲਤ ਦੇ ਕਾਰਨ ਬ੍ਰਾਂਡਾਂ ਦੁਆਰਾ ਤਰਜੀਹ ਦਿੱਤੀ ਜਾਂਦੀ ਹੈ. ਹਾਲਾਂਕਿ, ਥਰਮਲ ਟ੍ਰਾਂਸਫਰ ਟੈਕਨੋਲੋਜੀ ਵੀ ਅਕਸਰ ਸਬੰਧਤ ਗੁਣਵੱਤਾ ਦੀਆਂ ਸਮੱਸਿਆਵਾਂ ਦਾ ਸਾਹਮਣਾ ਕਰਦੀ ਹੈ. ਇਸ ਲੇਖ ਵਿਚ, ਅਸੀਂ ਕੁਝ ਆਮ ਗੁਣਾਂ ਦੀਆਂ ਸਮੱਸਿਆਵਾਂ ਅਤੇ ਹੱਲਾਂ ਦੀ ਸੂਚੀ ਦਿੰਦੇ ਹਾਂ.
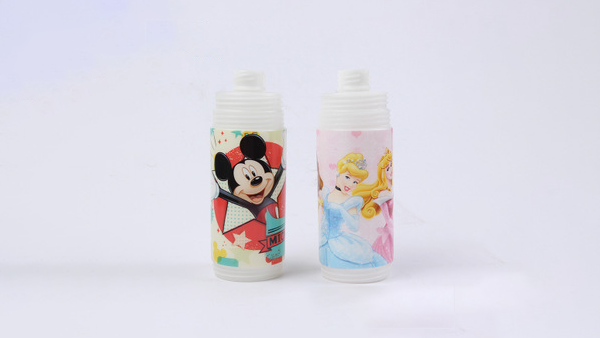
ਥਰਮਲ ਟ੍ਰਾਂਸਫਰ ਟੈਕਨੋਲੋਜੀ ਇਕ ਪ੍ਰਿੰਟਿੰਗ ਵਿਧੀ ਨੂੰ ਦਰਸਾਉਂਦੀ ਹੈ ਜੋ ਕਿ ਮਾਧਿਅਮ 'ਤੇ ਸਿਆਹੀ, ਦਬਾਅ ਦਾ ਮੁ tim ਲੇ ਸਿਧਾਂਤ ਨੂੰ ਸਿੱਧੇ ਤੌਰ' ਤੇ ਟਿਪਿਅਮ ਵਜੋਂ ਕਰਦੀ ਹੈ ਘਟਾਓਣਾ ਦੇ ਨਾਲ ਸਿਆਹੀ ਨਾਲ ਲੇਪੇਅਮ ਨਾਲ ਸੰਪਰਕ ਕਰੋ. ਥਰਮਲ ਪ੍ਰਿੰਟਿੰਗ ਦੇ ਸਿਰ ਅਤੇ ਪ੍ਰਭਾਵ ਰੋਲਰ ਦੇ ਹੀਟਿੰਗ ਅਤੇ ਦਬਾਅ ਦੁਆਰਾ, ਦਰਮਿਆਨੇ 'ਤੇ ਸਿਆਹੀ ਪੱਕੇ ਪ੍ਰਿੰਟਿਡ ਉਤਪਾਦ ਪ੍ਰਾਪਤ ਕਰਨ ਲਈ ਘਟਾਓ ਅਤੇ ਘਟਾਓ ਨੂੰ ਤਬਦੀਲ ਕਰ ਦੇਵੇਗੀ.
1, ਪੂਰਾ-ਪੇਜ ਫੁੱਲ ਪਲੇਟ
ਵਰਤਾਰੇ: ਚਟਾਕ ਅਤੇ ਪੈਟਰਨ ਪੂਰੇ ਪੇਜ 'ਤੇ ਦਿਖਾਈ ਦਿੰਦੇ ਹਨ.
ਕਾਰਨ: ਸਿਆਹੀ ਦਾ ਲੇਸ ਬਹੁਤ ਘੱਟ ਹੈ, ਸਕ੍ਰੈਪਰ ਦਾ ਕੋਣ ਗਲਤ ਹੈ, ਸਿਆਹੀ ਦਾ ਸੁੱਕਣਾ, ਸਥਿਰ ਬਿਜਲੀ, ਆਦਿ.
ਸਮੱਸਿਆ ਨਿਪਟਾਰਾ: ਲੇਸ ਨੂੰ ਵਧਾਓ, ਸਕੈਪਰ ਦੇ ਕੋਣ ਨੂੰ ਵਿਵਸਥਤ ਕਰੋ, ਕੱਟੇ ਹੋਏ ਏਜੰਟ ਨਾਲ ਫਿਲਮ ਦੇ ਪਿਛਲੇ ਹਿੱਸੇ ਨੂੰ ਪਹਿਲਾਂ ਤੋਂ ਰੱਖੋ.
2. ਖਿੱਚਣਾ
ਵਰਤਾਰੇ: ਕੋਟ ਵਰਗੇ ਲਾਈਨਾਂ ਪੈਟਰਨ ਦੇ ਇੱਕ ਪਾਸੇ ਦਿਖਾਈ ਦੇਣਗੀਆਂ, ਅਕਸਰ ਵ੍ਹਾਈਟ ਸਿਆਹੀ ਅਤੇ ਪੈਟਰਨ ਦੇ ਕਿਨਾਰੇ ਤੇ ਦਿਖਾਈ ਦਿੰਦੀਆਂ ਹਨ.
ਕਾਰਨ: ਸਿਆਹੀ ਪਿਗਮੈਂਟ ਕਣ ਵੱਡੇ ਹਨ, ਸਿਆਹੀ ਸਾਫ਼ ਨਹੀਂ ਹੈ, ਲੇਸ ਉੱਚ, ਸਥਿਰ ਬਿਜਲੀ, ਆਦਿ.
ਸਮੱਸਿਆ ਨਿਪਟਾਰਾ: ਸਿਆਹੀ ਫਿਲਟਰ ਕਰੋ ਅਤੇ ਇਕਾਗਰਤਾ ਨੂੰ ਘਟਾਉਣ ਲਈ ਖੁਰਚੇ ਨੂੰ ਹਟਾਓ; ਵ੍ਹਾਈਟ ਸਿਆਹੀ ਪ੍ਰੀ-ਤਿੱਖੀ ਕੀਤੀ ਜਾ ਸਕਦੀ ਹੈ, ਫਿਲਮ ਨੂੰ ਸਥਿਰ ਬਿਜਲੀ ਨਾਲ ਇਲਾਜ ਕੀਤਾ ਜਾ ਸਕਦਾ ਹੈ, ਅਤੇ ਸਕ੍ਰੈਪਰ ਅਤੇ ਪਲੇਟ ਨੂੰ ਤਿੱਖੀ ਚਾਪਲੂਸੀ ਬਣਾਇਆ ਜਾ ਸਕਦਾ ਹੈ.
3. ਮਾੜੀ ਰੰਗ ਰਜਿਸਟ੍ਰੇਸ਼ਨ ਅਤੇ ਬੇਨਕਾਬ ਤਲ
ਵਰਤਾਰੇ: ਜਦੋਂ ਕਈ ਰੰਗਾਂ ਦੀ ਅਦਾਇਗੀ ਹੁੰਦੀ ਹੈ, ਰੰਗ ਸਮੂਹ ਦਾ ਭਟਕਣਾ ਹੁੰਦਾ ਹੈ, ਖ਼ਾਸਕਰ ਬੈਕਗ੍ਰਾਉਂਡ ਰੰਗ 'ਤੇ.
ਮੁੱਖ ਕਾਰਨ: ਮਸ਼ੀਨ ਦੇ ਆਪ ਸ਼ੁੱਧ ਸ਼ੁੱਧਤਾ ਅਤੇ ਉਤਰਾਅ-ਚੜ੍ਹਾਅ ਹਨ; ਮਾੜੀ ਪਲੇਟ ਬਣਾਉਣਾ; ਅੰਦਰੂਨੀ ਰੰਗ ਦਾ ਗਲਤ ਵਿਸਥਾਰ ਅਤੇ ਸੁੰਗਣਾ.
ਸਮੱਸਿਆ ਨਿਪਟਾਰਾ: ਦਸਤੀ ਰਜਿਸਟਰ ਕਰਨ ਲਈ ਸਟ੍ਰੋਬ ਲਾਈਟਾਂ ਦੀ ਵਰਤੋਂ ਕਰੋ; ਦੁਬਾਰਾ ਪਲੇਟ ਕਰਨਾ; ਪੈਟਰਨ ਦੇ ਵਿਜ਼ੂਅਲ ਪ੍ਰਭਾਵ ਦੇ ਪ੍ਰਭਾਵ ਅਧੀਨ ਫੈਲਾਓ ਜਾਂ ਪੈਟਰਨ ਦੇ ਇੱਕ ਛੋਟੇ ਹਿੱਸੇ ਨੂੰ ਚਿੱਟਾ ਨਾ ਕਰੋ.
4. ਸਿਆਹੀ ਸਪਸ਼ਟ ਤੌਰ ਤੇ ਚੀਰ ਨਹੀਂ ਦਿੱਤੀ ਜਾਂਦੀ
ਵਰਤਾਰਾ: ਛਾਪੀ ਗਈ ਫਿਲਮ ਧੁੰਦਲੀ ਦਿਖਾਈ ਦੇ ਰਹੀ ਹੈ.
ਕਾਰਨ: ਸਕ੍ਰੈਪਰ ਫਿਕਸਿੰਗ ਫਰੇਮ loose ਿੱਲਾ ਹੈ; ਪਲੇਟ ਦੀ ਸਤਹ ਸਾਫ਼ ਨਹੀਂ ਹੈ.
ਸਮੱਸਿਆ ਨਿਪਟਾਰਾ: ਸਕ੍ਰੈਪਰ ਨੂੰ ਠੀਕ ਕਰੋ ਅਤੇ ਬਲੇਡ ਧਾਰਕ ਨੂੰ ਠੀਕ ਕਰੋ; ਪ੍ਰਿੰਟਿੰਗ ਪਲੇਟ ਨੂੰ ਸਾਫ਼ ਕਰੋ, ਅਤੇ ਜੇ ਜਰੂਰੀ ਹੋਵੇ ਤਾਂ ਡਿਟਰਜੈਂਟ ਪਾ powder ਡਰ ਦੀ ਵਰਤੋਂ ਕਰੋ; ਪਲੇਟ ਅਤੇ ਖੁਰਚੇ ਦੇ ਵਿਚਕਾਰ ਉਲਟਾ ਹਵਾ ਦੀ ਸਪਲਾਈ ਸਥਾਪਤ ਕਰੋ.
5. ਰੰਗ ਫਲੇਕਸ
ਵਰਤਾਰਾ: ਰੰਗ ਮੁਕਾਬਲਤਨ ਵੱਡੇ ਨਮੂਨੇ ਦੇ ਸਥਾਨਕ ਹਿੱਸਿਆਂ ਵਿੱਚ, ਖਾਸ ਕਰਕੇ ਛਾਪੇ ਜਾਂਦੇ ਗਲਾਸ ਅਤੇ ਸਟੀਲ ਦੇ ਪੂਰਵਜ ਫਿਲਮਾਂ ਤੇ.
ਕਾਰਨ: ਰੰਗ ਪਰਤ ਨੂੰ ਇਲਾਜ ਕੀਤੇ ਗਏ ਫਿਲਮ 'ਤੇ ਛਾਪਣ ਵੇਲੇ ਭੜਕਣ ਦੀ ਵਧੇਰੇ ਸੰਭਾਵਨਾ ਹੁੰਦੀ ਹੈ; ਸਥਿਰ ਬਿਜਲੀ; ਰੰਗ ਸਿਆਹੀ ਦੀ ਪਰਤ ਸੰਘਣੀ ਹੈ ਅਤੇ ਕਾਫ਼ੀ ਸੁੱਕਦੀ ਨਹੀਂ.
ਸਮੱਸਿਆ ਨਿਪਟਾਰਾ: ਤੰਦੂਰ ਦਾ ਤਾਪਮਾਨ ਵਧਾਓ ਅਤੇ ਗਤੀ ਨੂੰ ਘਟਾਓ.
6. ਮਾੜੀ ਤਬਦੀਲੀ ਦੀ ਤੇਜ਼ੀ ਨਾਲ
ਵਰਤਾਰਾ: ਘਟਾਓਣਾ ਵਿੱਚ ਤਬਦੀਲਤਮਕ ਰੰਗ ਪਰਤ ਆਸਾਨੀ ਨਾਲ ਟੈਸਟ ਟੇਪ ਦੁਆਰਾ ਖਿੱਚੀ ਜਾਂਦੀ ਹੈ.
ਕਾਰਨ: ਗਲਤ ਅਲੱਗ ਹੋਣਾ ਜਾਂ ਵਾਪਸ ਗੂੰਦ, ਮੁੱਖ ਤੌਰ 'ਤੇ ਘਟਾਓਣਾ ਨਾਲ ਮੇਲ ਨਹੀਂ ਖਾਂਦਾ.
ਸਮੱਸਿਆ ਨਿਪਟਾਰਾ: ਵਿਛੋੜੇ ਦੇ ਗਲੂ ਨੂੰ ਬਦਲੋ (ਜੇ ਜ਼ਰੂਰੀ ਹੋਵੇ ਤਾਂ ਵਿਵਸਥਤ ਕਰੋ); ਉਸ ਪਿਛਲੇ ਗਲੂ ਨੂੰ ਬਦਲੋ ਜੋ ਘਟਾਓਣਾ ਨਾਲ ਮੇਲ ਖਾਂਦਾ ਹੈ.
7. ਐਂਟੀ-ਸਟਿਕਿੰਗ
ਵਰਤਾਰਾ: ਸਿਆਹੀ ਪਰਤ ਤਿਆਗਣ ਦੌਰਾਨ ਬੰਦ ਹੋ ਜਾਂਦੀ ਹੈ, ਅਤੇ ਆਵਾਜ਼ ਉੱਚੀ ਹੁੰਦੀ ਹੈ.
ਕਾਰਨ: ਬਹੁਤ ਜ਼ਿਆਦਾ ਹਵਾ ਵਾਲਾ ਤਣਾਅ, ਸਿਆਹੀ ਦੇ ਅਧੂਰੇ ਸੁੱਕਣ, ਨਿਰੀਖਣ ਦੇ ਦੌਰਾਨ, ਅੰਦਰੂਨੀ ਅੰਦਰੂਨੀ ਤਾਪਮਾਨ ਅਤੇ ਨਮੀ, ਸਥਿਰ ਬਿਜਲੀ, ਬਹੁਤ ਤੇਜ਼ ਪ੍ਰਿੰਟਿੰਗ ਦੀ ਗਤੀ, ਆਦਿ.
ਸਮੱਸਿਆ ਨਿਪਟਾਰਾ: ਹਵਾਬਾਜ਼ੀ ਦੇ ਤਣਾਅ ਨੂੰ ਘਟਾਓ, ਜਾਂ ਛਪਾਈ ਦੀ ਗਤੀ ਨੂੰ ਘਟਾਓ, ਸੁੱਕਣ ਵਾਲੇ ਤਾਪਮਾਨ ਅਤੇ ਨਮੀ ਨੂੰ ਨਿਯੰਤਰਣ ਕਰੋ, ਅਤੇ ਸਥਿਰ ਏਜੰਟ ਤੋਂ ਪਹਿਲਾਂ ਤੋਂ ਲਾਗੂ ਕਰੋ.
8. ਬਿੰਦੀਆਂ ਨੂੰ ਛੱਡਣਾ
ਵਰਤਾਰੇ: ਅਨਿਯਮਿਤ ਲੀਕਿੰਗ ਬਿੰਦੀਆਂ ਘੱਟ ਜਾਲਾਂ ਤੇ ਦਿਖਾਈ ਦਿੰਦੀਆਂ ਹਨ (ਬਿੰਦੀਆਂ ਦੇ ਸਮਾਨ ਨਹੀਂ).
ਕਾਰਨ: ਸਿਆਹੀ ਨਹੀਂ ਰੱਖੀ ਜਾ ਸਕਦੀ.
ਸਮੱਸਿਆ-ਨਿਪਟਾਰਾ: ਲੇਆਉਟ ਸਾਫ਼ ਕਰੋ, ਇਲੈਕਟ੍ਰੋਸਟੇਟਿਕ ਸਿਆਹੀ ਚੂਸਣ ਰੋਲਰ ਦੀ ਵਰਤੋਂ ਕਰੋ, ਬਿੰਦੀਆਂ ਨੂੰ ਡੂੰਘਿਤ ਕਰੋ, ਅਤੇ ਬਿਨਾਂ ਹੋਰ ਸ਼ਰਤਾਂ ਨੂੰ ਬਿਨਾਂ ਸਹੀ ਤਰੀਕੇ ਨਾਲ ਘਟਾਓ.
9. ਸੰਤਰੇ ਦੇ ਛਿਲੋ ਵਰਗੇ ਲਹਿਰਾਂ ਜਦੋਂ ਸੋਨਾ, ਚਾਂਦੀ ਅਤੇ ਮੋਤੀ ਸੰਪੂਰਣ ਦਿਖਾਈ ਦਿੰਦੇ ਹਨ
ਵਰਤਾਰਾ: ਸੋਨਾ, ਚਾਂਦੀ ਅਤੇ ਮੋਤੀ ਆਮ ਤੌਰ 'ਤੇ ਵੱਡੇ ਖੇਤਰ' ਤੇ ਸੰਤਰੇ ਦੇ ਛਿਲੇ ਵਰਗੇ ਲਹਿਰੇ ਹੁੰਦੇ ਹਨ.
ਕਾਰਨ: ਸੋਨੇ, ਚਾਂਦੀ ਅਤੇ ਮੋਤੀ ਦੇ ਕਣ ਵੱਡੇ ਹੁੰਦੇ ਹਨ ਅਤੇ ਇਸ ਨੂੰ ਅਕਹਿ ਘਣਤਾ ਦੇ ਨਤੀਜੇ ਵਜੋਂ ਫੈਲਿਆ ਨਹੀਂ ਜਾ ਸਕਦਾ.
ਸਮੱਸਿਆ ਨਿਪਟਾਰਾ: ਛਾਪਣ ਤੋਂ ਪਹਿਲਾਂ, ਸਿਆਹੀ ਨੂੰ ਇਕਸਾਰ ਕਰੋ, ਸਿਆਹੀ ਟਰੇ 'ਤੇ ਸਿਆਹੀ ਪੰਪ ਕਰੋ, ਅਤੇ ਸਿਆਹੀ ਟਰੇ' ਤੇ ਪਲਾਸਟਿਕ ਏਅਰ ਵਰੇਜ ਲਗਾਓ; ਪ੍ਰਿੰਟਿੰਗ ਦੀ ਗਤੀ ਨੂੰ ਘਟਾਓ.
10. ਪ੍ਰਿੰਟ ਕੀਤੀਆਂ ਪਰਤਾਂ ਦੀ ਮਾੜੀ ਪ੍ਰਜਨਨ
ਵਰਤਾਰੇ: ਲੇਅਰਾਂ ਵਿੱਚ ਬਹੁਤ ਵੱਡੇ ਰੂਪ ਵਿੱਚ ਇੱਕ ਤਬਦੀਲੀ ਵਾਲੇ ਪੈਟਰਨ (ਜਿਵੇਂ ਕਿ 15% -100%) ਅਕਸਰ ਹਲਕੇ-ਟੂਨ ਦੇ ਹਿੱਸੇ ਵਿੱਚ ਛਾਪਣ ਵਿੱਚ ਅਸਫਲ ਰਹਿੰਦੇ ਹਨ, ਜਾਂ ਸਪੱਸ਼ਟ ਦੇ ਨਾਲ ਮਿਡਲ ਟੋਨ ਦੇ ਹਿੱਸੇ ਦੇ ਜੰਕਸ਼ਨ ਤੇ ਨਾਕਤਾ ਹਲਕੇ ਅਤੇ ਹਨੇਰਾ.
ਕਾਰਨ: ਬਿੰਦੀਆਂ ਦੀ ਤਬਦੀਲੀ ਦੀ ਰੇਂਜ ਬਹੁਤ ਵੱਡੀ ਹੈ, ਅਤੇ ਸਿਆਹੀ ਫਿਲਮ ਨੂੰ ਮਾੜੀ ਅਡੇਸਿਜ਼ੀ ਹੈ.
ਸਮੱਸਿਆ ਨਿਪਟਾਰਾ: ਇੱਕ ਇਲੈਕਟ੍ਰੋਸਟੈਟਿਕ ਸਿਆਹੀ-ਜਜ਼ਬ ਕਰਨ ਵਾਲੀ ਰੋਲਰ ਦੀ ਵਰਤੋਂ ਕਰੋ; ਦੋ ਪਲੇਟਾਂ ਵਿੱਚ ਵੰਡੋ.
11. ਪ੍ਰਿੰਟ ਕੀਤੇ ਉਤਪਾਦਾਂ ਤੇ ਹਲਕੇ ਗਲੋਸ
ਵਰਤਾਰੇ: ਪ੍ਰਿੰਟਿਡ ਉਤਪਾਦ ਦਾ ਰੰਗ ਨਮੂਨੇ ਤੋਂ ਹਲਕਾ ਹੈ, ਖ਼ਾਸਕਰ ਜਦੋਂ ਚਾਂਦੀ ਦੀ ਛਪਾਈ.
ਕਾਰਨ: ਸਿਆਹੀ ਦੀ ਲੇਸ ਬਹੁਤ ਘੱਟ ਹੈ.
ਸਮੱਸਿਆ ਨਿਪਟਾਰਾ: ਸਿਆਹੀ ਦੇ ਲੇਸ ਨੂੰ appropriate ੁਕਵੀਂ ਰਕਮ ਵਧਾਉਣ ਲਈ ਅਸਲ ਸਿਆਹੀ ਸ਼ਾਮਲ ਕਰੋ.
12. ਚਿੱਟੇ ਪਾਤਰ ਦੇ ਕਿਨਾਰੇ ਜੱਫੀ ਪਾਏ ਜਾਂਦੇ ਹਨ
ਵਰਤਾਰਾ: ਜੱਗੇਡ ਕਿਨਾਰੇ ਅਕਸਰ ਉੱਚ ਚਿੱਟੇਪਣ ਦੀਆਂ ਜ਼ਰੂਰਤਾਂ ਵਾਲੇ ਪਾਤਰਾਂ ਦੇ ਕਿਨਾਰਿਆਂ ਤੇ ਦਿਖਾਈ ਦਿੰਦੇ ਹਨ.
ਕਾਰਨ: ਸਿਆਹੀ ਦਾ ਦਾਣਾ ਅਤੇ ਰੰਗਤ ਕਾਫ਼ੀ ਵਧੀਆ ਨਹੀਂ ਹਨ; ਸਿਆਹੀ ਦੀ ਲੇਸ ਘੱਟ ਹੈ, ਆਦਿ.
ਖਾਤਮੇ: ਚਾਕੂ ਨੂੰ ਤਿੱਖਾ ਕਰਨਾ ਜਾਂ ਜੋੜਨਾ; ਸਕ੍ਰੈਪਰ ਦੇ ਕੋਣ ਨੂੰ ਵਿਵਸਥਿਤ ਕਰਨਾ; ਸਿਆਹੀ ਦੇ ਲੇਸ ਨੂੰ ਵਧਾਉਣਾ; ਇੱਕ ਲੇਜ਼ਰ ਪਲੇਟ ਵਿੱਚ ਬਿਜਲੀ ਦੇ ਉੱਕਰੀ ਪਲੇਟ ਨੂੰ ਬਦਲਣਾ.
13. ਸਟੀਲ (ਸਿਲੀਕਾਨ ਪਰਤ) ਦੀ ਪੂਰਵ-ਕੋਸੇ ਵਾਲੀ ਫਿਲਮ ਦਾ ਅਸਮਾਨ ਪਰਤ)
ਸਟੇਨਲੈਸ ਸਟੀਲ ਦੀ ਟ੍ਰਾਂਸਫਰ ਫਿਲਮ ਦੀ ਛਾਪਣ ਤੋਂ ਪਹਿਲਾਂ, ਤਬਾਦਲੇ ਦੀ ਪ੍ਰਕਿਰਿਆ ਦੇ ਦੌਰਾਨ ਸਿਆਹੀ ਪੱਕੇ ਪੇਟਿੰਗ (ਜਦੋਂ ਤਾਪਮਾਨ 145 ਡਿਗਰੀ ਸੈਲਸੀਅਸ ਤੋਂ ਉਪਰ ਹੈ, ਇਸ ਨੂੰ ਛਿਲਣਾ ਮੁਸ਼ਕਲ ਹੁੰਦਾ ਹੈ ਫਿਲਮ 'ਤੇ ਸਿਆਹੀ ਪਰਤ).
ਵਰਤਾਰਾ: ਫਿਲਮ 'ਤੇ ਸਤਰਾਂ ਅਤੇ ਹੁਕਮ ਹਨ.
ਕਾਰਨ: ਨਾਕਾਫ਼ੀ ਤਾਪਮਾਨ (ਸਿਲੀਕਾਨ ਦਾ ਨਾਕਾਫੀ ਸੜਨ), ਗਲਤ ਘੋਲਨ ਵਾਲਾ ਅਨੁਪਾਤ.
ਖਾਤਮੇ: ਓਵਨ ਦਾ ਤਾਪਮਾਨ ਇੱਕ ਨਿਸ਼ਚਤ ਉਚਾਈ ਤੱਕ ਵਧਾਓ.
ਪੋਸਟ ਸਮੇਂ: ਜੁਲਾਈ -03-2024